Yachting World
- Digital Edition
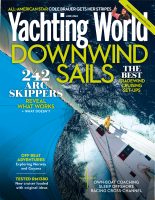

How (and why) wood is making a comeback in yacht building
- Rupert Holmes
- May 30, 2023
Rupert Holmes reports on latest developments in wooden yacht construction, and why this ancient material is being used for hi-tech contemporary design
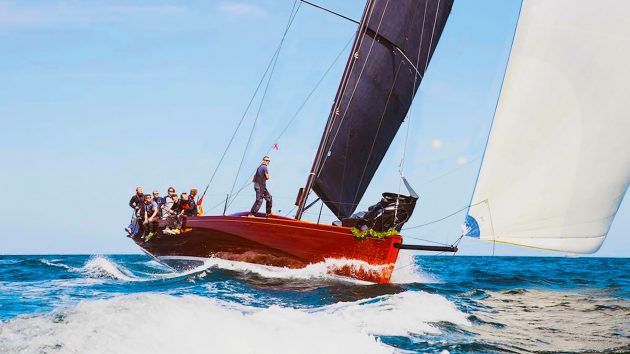
Why would a naval architect and structural engineer used to working with cutting edge materials for America’s Cup teams, including INEOS Britannia , and companies like Airbus, be excited about working with wood?
“It’s quite simple for me,” says French designer Thomas Tison, “Modernity does not neglect where we all come from – on the contrary it makes the best of it. In a way a boat is a heritage, so to ignore wood would be to ignore the essence of yacht design and building.
“Carbon fibre is only an evolution from this heritage and reinstating wood as a modern material increases the number of options a naval architect has for creation and performance.”
Tison designed the stunning, contemporary 48ft offshore racer Elida which launched last year, and currently has a timber/epoxy 40ft high-end daysailer on the drawing board. To optimise Elida ’s weight and stiffness Tison tested three different timber and glue laminates at an Airbus facility. “What we found was very interesting,” he told me. “The existing data was 20 years old, but now we can carefully select the glue and timber, so the figures for our laminates were stiffer than predicted, with the sitka spruce an order of magnitude better than expected.”
Elida is built of diagonally planked sitka spruce covered with a 3mm mahogany veneer. Additional internal stiffening is provided by local layers of 200g carbon fibre. The result is a very stiff structure – projected forestay loads match those used on TP52s, yet the total weight of the 48ft hull shell is only 1,000kg.
Tison’s next project is a very high end 40ft daysailer. Construction will be an evolution of Elida ’s, giving a strong and stiff structure that meets Category A requirements, yet total displacement is only 3,700kg. He also has a concept under way for a 45m superyacht built in a similar manner.
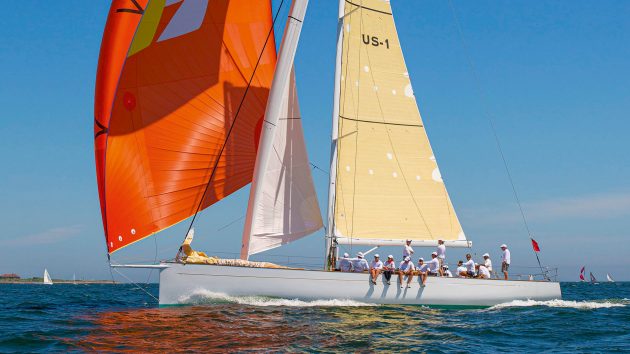
Outlier is a cold-molded custom 55-footer designed by Botin. Photo: Billy Black
Traditional skillset
The enthusiasm naval architects young and old have for wood/epoxy composite construction is striking. Many of today’s stand-out new designs on both sides of the Atlantic are built this way and it’s often the best option for one off builds and short production runs. Key advantages include stunning aesthetics, stiff, lightweight structures and excellent longevity.
Today British yard Spirit Yachts is perhaps the most well-known specialist in this form of construction and their wood-as-art concept is well documented, including the sculptural approach taken with the Spirit 111 Geist . However, examples of other yachts abound, including Rob Humphreys’ Tempus 90 superyacht. This was built in Turkey, which unlike many countries never lost its wooden-boat building industry. As a result plenty of yards today are familiar with working with epoxy/timber composites. And many other top-notch recent wooden yachts have been built there, ranging right up to superyacht size, including Andre Hoek’s PC Yacht range and a number of his Truly Classic designs.
Britain has its own strong tradition of wooden-built designs: the Elephant Boatyard on the River Hamble has a long history of building, and maintaining, timber/epoxy yachts, including the Barracuda 45 built for Bob Fisher in the late 1980s.
Wood was the medium successful IRC raceboat designer John Corby made his name with in the 1990s and 2000s. And it was the choice of one of the UK’s most successful yacht designers, Stephen Jones, for his own 46ft one-off Meteor , launched in 2006. She was built in Grimsby by Farrow and Chambers, which also built two cedar epoxy yachts for former Yachting World editor Andrew Bray.
On the other side of the Atlantic, several New England yards are active in building new custom and semi-custom yachts in wood/epoxy. Notable recent examples include the Lyman-Morse 46, Brooklin Boat Yard’s Jim Taylor-designed 44ft Equipoise , and the Botin custom 55-footer Outlier . A long list of other notable recent launches include Anna , a 65ft Stephens Waring design built by Lyman-Morse and launched in 2020.

The beauty of wood inside a hand-crafted Spirit. Photo: Paul Wyeth
Build techniques
UK-based designer Rob Humphreys has a long association with this build method, having designed his first vessel in wood in the late 1970s, followed by a string of others, from 22-footers to superyachts, over the following decades. Humphreys remains keen to design more: “The only thing that’s holding us back really is an issue of market education,” he told me.
The medium is often poorly understood, with few people realising the benefits and many assuming it has the same drawbacks as traditional timber construction, or that the technology hasn’t moved on since cold-moulded wooden boats of the 1960s. These were built with resorcinol glues that were originally developed in the early 1940s, but required considerable clamping pressure to create a reliable bond and couldn’t be used as a coating to protect timber.
The epoxy revolution, driven enthusiastically by brothers Meade, Joel, and Jan Gougeon in Michigan in the early 1970s, marked a turning point for boatbuilding. “They got chemists to reconfigure epoxy to be runny enough to saturate the wood rather like a varnish,” explains Stephen Jones.
Even though epoxy doesn’t penetrate deep below the surface of timber, it sticks so well that, unlike paint and varnish, it forms a genuine barrier that keeps water out of the timber in the long term. As a result these boats have potential to last as long as any fibreglass structure.
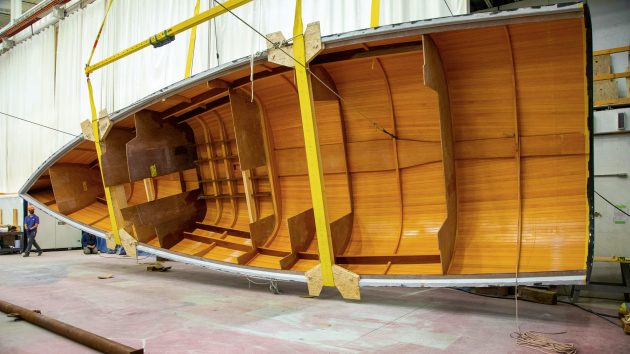
Lyman-Morse 46 hull completed and being turned outside the boat shed. Photo: Alison Langley/Lyman-Morse
There was another key advantage. “It could also be thickened as required for glueing and, most importantly, gap filling,” adds Jones. This significantly speeds up the build process. These vessels are generally inherently stiffer and lighter than conventionally built fibreglass yachts and it was a preferred build method for performance yachts before cored composites became reliable.
Meade Gougeon’s 35ft trimaran Adagio , launched in 1970, was the first large all epoxy bonded and sealed wooden boat built without the use of mechanical fasteners (and is still sailing on the Great Lakes over 40 years on). Three years later the brothers built the Ron Holland-designed 41ft IOR Two Tonner Golden Dazy , ahead of a slew of further designs including a 60ft trimaran for Phil Weld’s 1980 OSTAR single-handed transatlantic race , before race organisers imposed an upper size limit. Weld subsequently had the 50ft timber/epoxy tri Moxie built by Walter Greene, in which he won the OSTAR.
Over the years precise construction methods have varied, although all but a handful of boats are built with several layers of timber with the grain running in different directions to create a stiff structure. Some have a purely cold moulded construction, with larger boats often employing four or more layers laid at around 90° to each other. This creates a lightweight and stiff structure that can be protected from impact damage with epoxy and glass cloth. The Lyman-Morse 46, for instance, is built of four layers of vacuum glued Douglas fir and western red cedar.
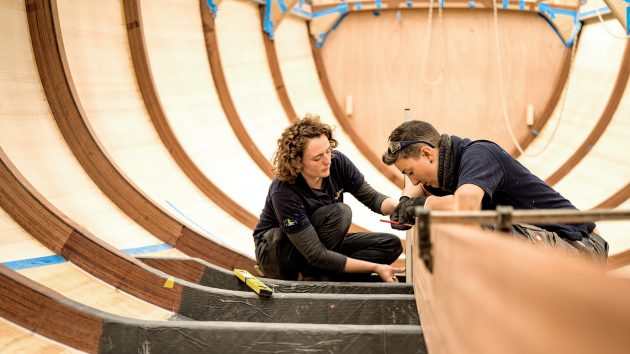
Hand-built expertise at the Spirit yard in Suffolk. Photo: Spirit Yachts
Others start with a layer of narrow planks, termed strip planking. This had been a construction method long before the use of epoxy, but it became much more popular thanks to the development of the Speed Strip technique by Sunderland timber merchant Joseph Thompson & Co (now renamed NYTimber) with help from Farrow and Chambers. The planks have a loose tongue and groove profile, allowing them to neatly conform to the hull shape and giving space for thickened epoxy glue.
Speed Strip also eliminated the need for scarfs to be cut where planks are joined and reduced the number of mechanical fasteners needed. This reduced planking time by a quarter, and clean up and fairing time by 70%. An additional advantage, Jones says, is the “predominance of fore and aft timber strips/planks increases global hull stiffness – the ability of the hull to resist rig loads.”
Around the same time Humphreys was also working on ways to reduce build times. The hull of his H22 sportsboat, which was available as a flat-pack kit with CNC cut components, could be assembled from scratch in a few hours by one person. I know of 40ft offshore racing yachts that were planked up in a week.
Strip planked boats can be built over laminated frames that become part of the final structure, and don’t require a mould that is subsequently discarded. These frames are surprisingly quick and easy to create – at Spirit Yachts, for instance, they’re assembled on full-size print outs of the boat’s plans laid over a plywood floor. This allows each piece of timber to be bent by hand into exactly the right shape and held in place using spikes driven into the floor. They’re then clamped together in situ while the epoxy cures.
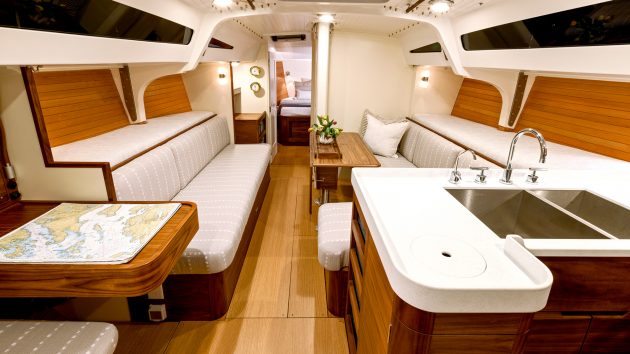
The Lyman-Morse 46 interior shows off its timber construction, with plenty of white painted surfaces for an airy feel. Photo: Alison Langley/Lyman-Morse
Originally cedar was used for Speed Strip planks as it’s lightweight yet very resistant to rot, although other species with similar properties, including Douglas fir and sitka spruce, are also suitable. Typically two thinner outer layers of double-diagonal planking are added outside the strip planking.
In the case of Zest , our 36ft Rob Humphreys design built by Farrow and Chambers in 1992, this forms a 20mm-thick tri-axial construction with the grain of the timber oriented in three different directions. Larger yachts may have four or more layers outside the strip planking and a few boats have an additional transverse skin to help strengthen the area around the keel.
Impact protection
In all cases the whole lot is glued together and sealed from water ingress with epoxy. Therefore no more maintenance is needed than for a fibreglass hull and it will never succumb to osmosis.
Jim Taylor, designer of the 44ft Equipoise and 50ft Rascal , both recently built by Brooklin Boat Yard in Maine, says that in North America this construction is likely to be referred to as cold moulded, with the term referring to the outer layers, rather than the inner skin of strip planks.
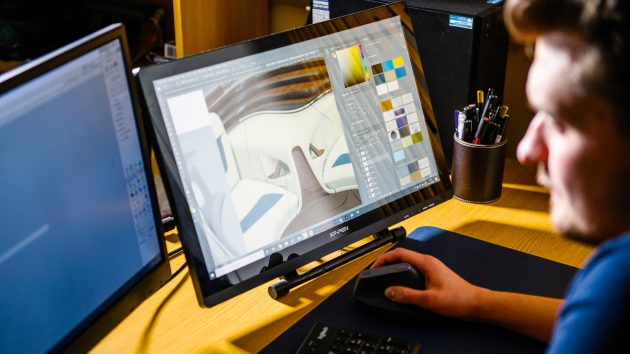
Modern wooden builds created using latest CAD at Spirit Yachts. Photo: Spirit Yachts
Equipoise was built with a first layer of fore-and-aft tongue and groove larch planking which is epoxy bonded to the laminated keel, keel floors, bulkheads and ring frames. Outside of that two layers of diagonal 3/16in (5mm) paulonia were vacuum bagged at +/-45° to the initial planking. Then a further layer of tongue and groove larch was laminated over the paulonia, again in a fore and aft orientation. Outside that is a protective layer of epoxy/glass. Displacement is little more than six tonnes, despite an unusually large 44% ballast ratio, allowing a large rig without the drawbacks of excessive draught.
“There is a whole lot to like about this type of construction,” Taylor says. “The approach is cost effective and the result is extremely attractive on many levels. The boats are light, strong, tough, quiet and well insulated thermally. A bright finished inside skin can be integrated into an especially elegant interior, the construction materials are environmentally sustainable, and there’s not a lot of waste. They’re not as light as carbon skins over lightweight core, but they are much more liveable and not nearly as fragile or as expensive.”
The outer glass/epoxy sheathing can vary from light cloth for impact protection, through to heavier laminates that add structural strength in high load areas such as around the keel. A few boats have glass only outside, rather than additional layers of timber, but these heavier laminates need more work and filler to create a fair surface.
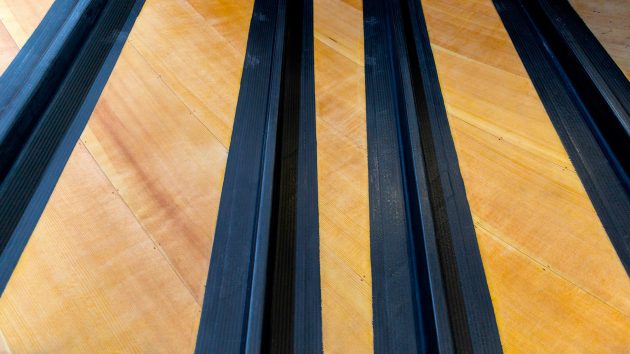
Carbon stiffening for Elida. Photo: Emeric Jezequel
Of course, if the outer sheathing is punctured, then it will need to be repaired quickly, but a quick application of epoxy filler is all that’s needed until a neat long-term repair can be made.
Developments and refinements over time include vacuum bagging the various layers of timber together, along with the external protective layers of glass cloth. At the high end carbon reinforcement is increasingly used strategically to add further stiffness where necessary, without a significant weight penalty.
Elida ’s varnished topsides look stunning, while those of the 1987 Humphreys-designed Apriori and 1988-built Old Mother Gun of 1988 still look great. There’s therefore a huge temptation for anyone building a wooden yacht to opt for similar finishes. However, it’s important to note in these cases the epoxy needs a more traditional varnish for UV protection and that can require a lot of maintenance. On the other hand, today’s polyurethane paints can last up to a decade in dark colours and Meteor ’s original white paint from 2006 still looks almost new.
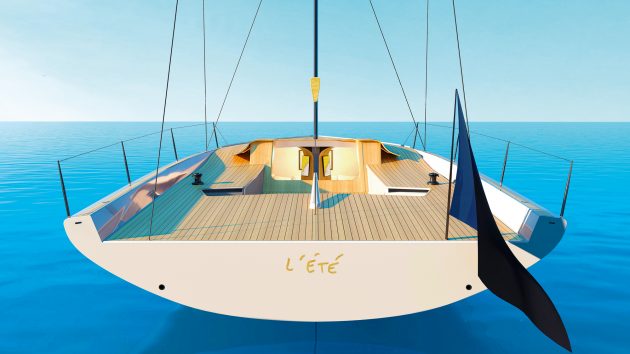
L’Été is a new 40ft daysailer design by Thomas Tison.
Modern look
On the other hand, varnished bright work on deck and coachroof sides are subject to less wear and tear than topsides. Jones says these are easy to prep for varnishing if designed with simple surfaces without fiddly detail. The cleaner style of modern classic deck structures also reduces water retention, so surfaces dry quickly. “It can still look the part but becomes less onerous to keep,” says Jones.
Below decks it’s easy to fall into a trap of showing off so much natural timber that the interior becomes dark; a strategic mix of white painted panels and clear timber finishes gives a much brighter result. The Spirit 72 , for instance, has satin painted panels and a carefully planned LED lighting system to enhance the warmth of the natural timber.
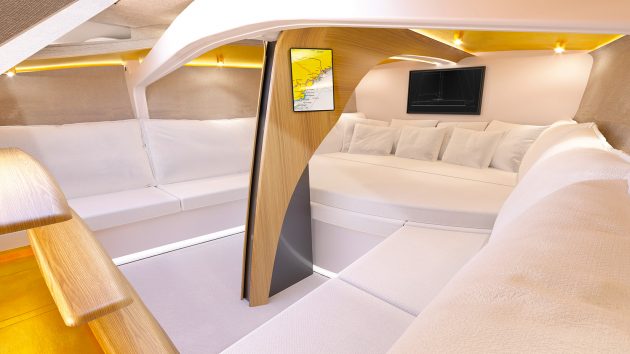
The Spirit 111 has a sculptural cockpit and interior. Photo: Spirit Yachts
Hull windows are possible and, even if maintaining a classic external appearance is a priority, it’s possible to allow a lot of light in from the deck. Spirit Yachts’ trademark fantail window is an excellent example of this.
Alternatively, interiors can be absolutely contemporary in style, as seen in RM Yachts’ 29-43ft range of plywood/epoxy performance cruisers. Plywood also offers excellent stiffness in relation to weight and is an ideal medium for today’s chined hull shapes. At RM all the pieces for an entire boat are delivered on pallets, ready for immediate assembly. Hulls are built over frames of substantial chipboard set up on jigs. Assembling a hull is therefore a straightforward process that doesn’t require a full mould.
The Ace 30 scow bow short-handed IRC raceboat also employs plywood/epoxy construction. It’s an approach the builder says considerably reduces the carbon footprint of building each boat.
Matt Newland of Swallow Yachts tells me their Whisper 300 retro-style planing motor cruiser has demonstrated that at sizes above 30ft an epoxy/timber construction can compete directly on labour hours with conventional fibreglass boatbuilding. The company’s next model, the Bay Cruiser 32, will be a traditionally styled, but very lightweight and quick, 32ft trailerable weekender made of clinker-style plywood and epoxy.
Other forthcoming projects include a range of 45-70ft modern classics by Stephen Jones and illustrator/designer Jonty Sherwill that will be built by the Elephant Boatyard.
These boats will also be more sustainable than their contemporaries built using conventional glass fibre or more advanced composites. The quantity of epoxy used for the build is small and bio-sourced resins can be used without the requirement for a full size mould. The result is that the carbon footprint associated with building the Ace 30, for instance is 1.9 tonnes, but would be more than three times that value for a boat of conventional construction, even before accounting for building the moulds.
If you enjoyed this….
Yachting World is the world’s leading magazine for bluewater cruisers and offshore sailors. Every month we have inspirational adventures and practical features to help you realise your sailing dreams. Build your knowledge with a subscription delivered to your door. See our latest offers and save at least 30% off the cover price.
Practical Boat Owner
- Digital edition
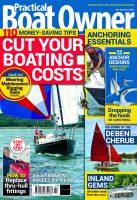
Boat wood: a complete guide for yacht owners
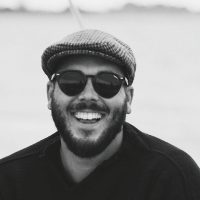
- lyndonmarch
- November 2, 2023
Boatbuilder and finisher Lyndon March explains which types of wood work best for different repairs and modifications on board
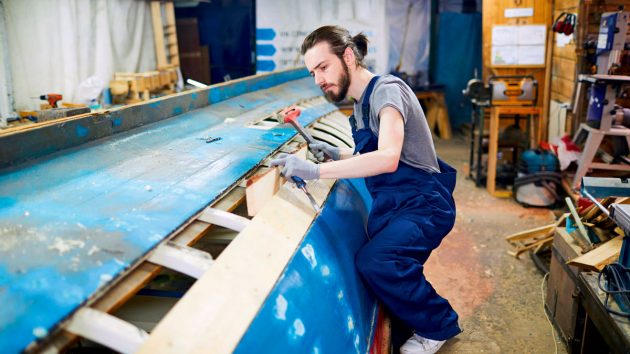
Whether you’re building a boat from scratch or making repairs, knowing which wood will work best for the job is essential. Credit: Dmitriy Shironosov/Alamy Credit: Dmitriy Shironosov/Alamy
Repairs, replacements and restorations are very much part and parcel of boat ownership.
At some point most of us will have to tackle a small, niggling woodwork repair ourselves, or undertake a larger-scale project.
However, are you making the correct choices when it comes to choosing the timber to use?
Like most items associated with boats, there is not a definitive right or wrong approach, but guidance is useful.
We often think of stout working boats as built of larch or oak and finer yachts dripping in teak and mahogany.
This is not always the golden rule though.
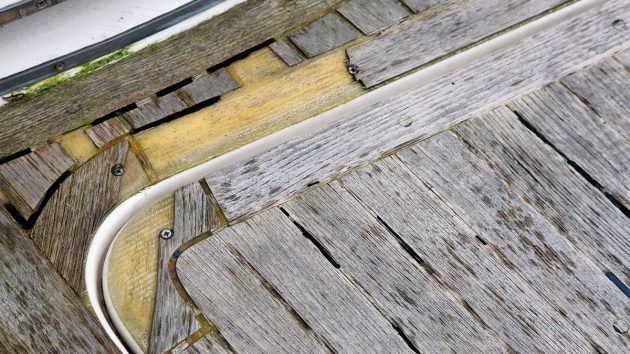
You may be able to source reclaimed teak to make repairs to small areas of deck
It’s worth keeping in mind the three key points when looking for the right wood for your project: durability, movement and structural integrity.
If your choice in material is informed by these golden rules you can make smart decisions and execute a lasting repair or update to your vessel.
Most commonly it’s the high-impact areas of a boat that require renewing, like grab rails, rubbing strakes and toe rails.
Exposed, vulnerable and rarely finished with more than a simple oil, these are the parts of the vessel that take a pounding during the season, doing very little for the longevity of the timber.
For most craft manufactured pre-1990, these areas will almost certainly be made of teak.
Owners are advised to look after teak with careful cleaning to increase its life, especially as teak is scarce.
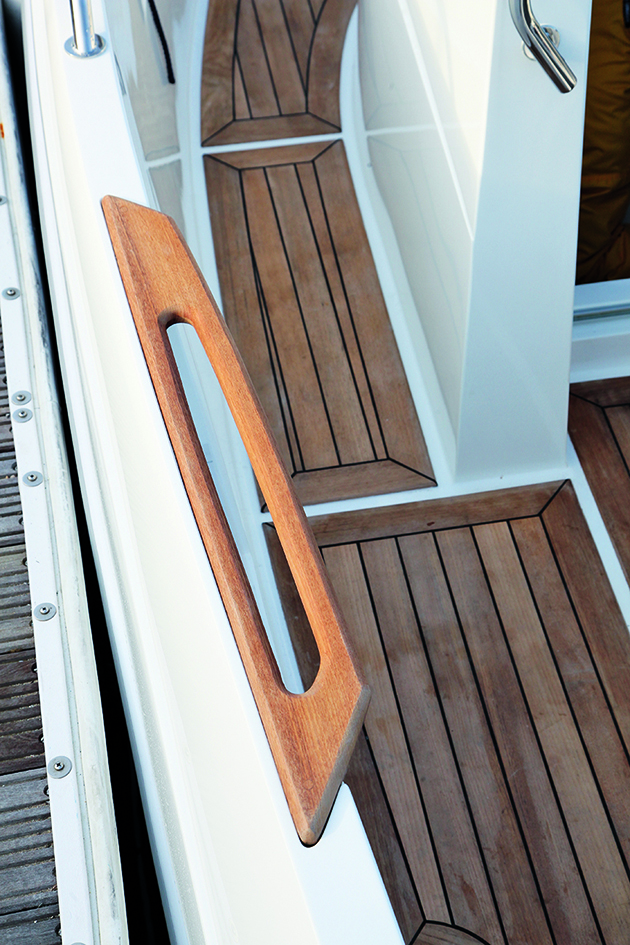
Grab rails and toe rails are often made of teak, so look after them. Credit: William Payne Photography
However, if it does need replacing, you may be able to grab a bargain on the second-hand market, given the small amount of wood you’re likely to need.
Teak is a wonderful material, with an ability to weather gently and an almost self-oiling quality.
It also fits all of our key points – scoring highly on durability and movement as well as structural integrity.
Teak can also be used almost anywhere in a vessel; as demonstrated in my own 1901 rowing dinghy which is entirely built of teak.
Fortunately, but not without some hunting around, there are small quantities of teak still lurking in timber yards around the country, and certain specialists such as Trinity Marine carry stocks of reclaimed teak; however, it is expensive and requires some careful machining to minimise wastage.
There are big challenges in sourcing teak which is legal and ecologically sustainable.
Boat wood: Alternatives to teak
Being realistic about the affordability of the wonderful oily teak forces us to look within the mahogany family or iroko.
Both meet our three golden rules; with iroko giving us a bit more structural integrity and providing much more durability in the weather if left uncoated or oil finished.
Khaya, sapele and utile mahoganies will easily hold up as toe rails and rubbing strakes and, much like iroko, give us wonderful grain results but really require a varnish to add protection and longevity.
A future world without the availability of teak forces us to look at other areas of our vessels that might need repairs; decks, cockpit gratings , hatches and skylights.
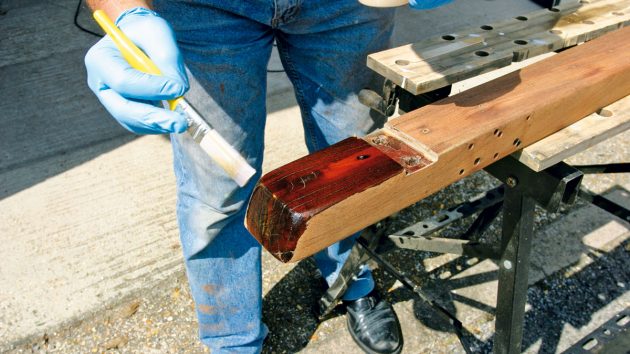
Mahogany needs varnishing in order to protect the wood and increase longevity
If these are teak, then it pays to look after them.
Those of us fortunate enough not to have a traditional laid deck might still have deck planking or at least deck coverings.
It’s not uncommon for vessels to have a teak-clad deck or at least some teak trim, pulpit perches or cockpit locker lids.
Years of enthusiastic deck scrubbing, clumsy feet, or gentle sanding often leave teak decks in a bad state of repair, with the screw plugs barely hanging on for life.
For smaller sections, you may be able to hunt down some elusive teak but for bigger areas of decking, you’ll need to look for an alternative.
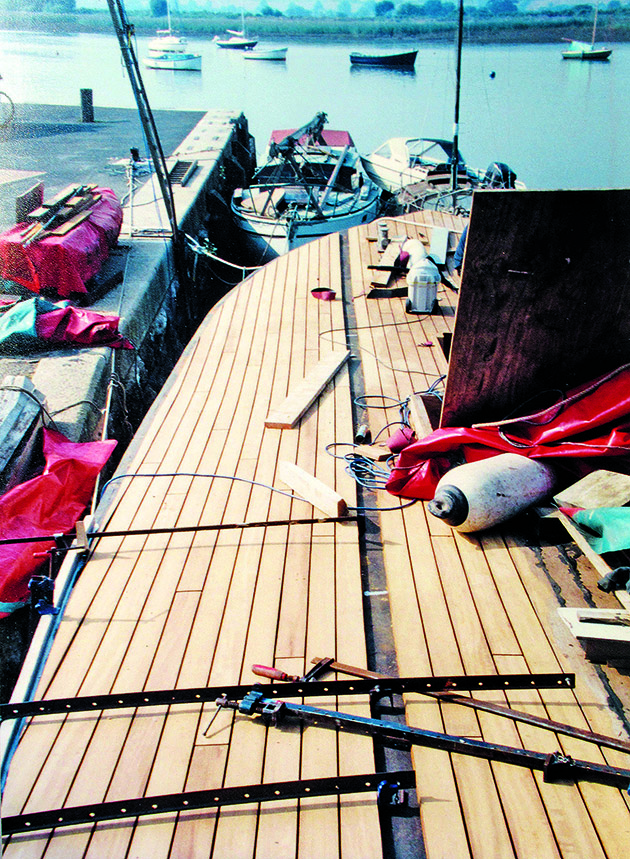
Iroko can be matched to existing teak, which makes it ideal for decking. Credit: Hazel McCabe
Iroko could be the perfect alternative to teak. Unfortunately, it’s not particularly nice to work with and some people have suffered allergic reactions to it, so it’s advisable to don personal protective equipment (PPE) when working with iroko.
Iroko can, however, provide you with a teak-style of deck that should give a hardly noticeable match to existing teak.
It can be left to weather or be oiled and varnished with stunning results.
If you’re replacing a large area, or laying all new decking , I’d recommend taking some inspiration from the working boat scene.
Douglas fir or larch are easy to machine and suitable for glueing to a subdeck.
They meet nearly all of the three golden rules, and age to a lovely even-weather grey colour, much like untreated teak.
Both are also soft underfoot for those barefoot sailors among us.
But they do have one disadvantage: neither last as well as teak, with maybe a 10- to 15-year lifespan depending on how well the wood has been cared for.
Keeping boat wood healthy
On a well-kept and regularly sailed vessel, it’s unusual to find fungal issues on deck timbers and fittings – a regular dousing of salt water tends to keep this problem at bay.
Deck fixtures, however, tend to suffer from wearing out or damage and occasionally UV-related issues.
The less saturated and inaccessible sections of our boats can play host to fungi; even wonderfully oiled teak and varnished mahogany can be no match for a lack of ventilation.
Mast foots, cockpit lockers, cabin soles and interior joinery all suffer.
Mostly it’s cost-effective to replace like for like.
Most vessels have been fitted out with hardwood-trimmed plywood panels bonded together and then bonded to the vessel.
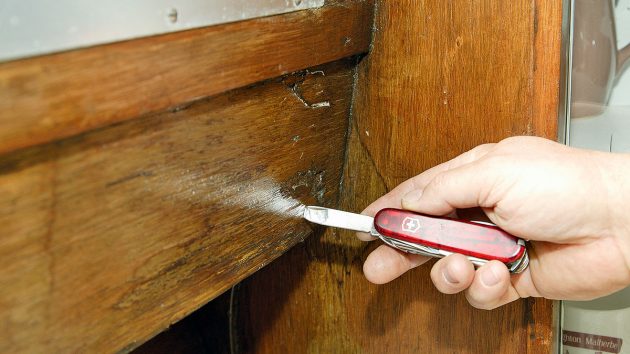
In areas of little ventilation, wood can rot. It is usually best to replace like for like
This is still a great approach, as plywood is simple to bond and use, as well as providing structural integrity, movement and durability.
It also means that huge amounts of extra internal weight are not being added down below; important for a well-balanced boat.
We shouldn’t just limit ourselves to painted white plywood with hardwood trim.
The replacement of interior joinery gives us a chance to amplify the space, and there are lots of kits and tutorials on how to add a veneer or carbon wrap to your plywood.
No matter how large or small the repair is, you should consider ventilation in the area where the wood is being replaced.
Look at coating the edges of the plywood and investing in marine-grade quality plywood.
Continues below…
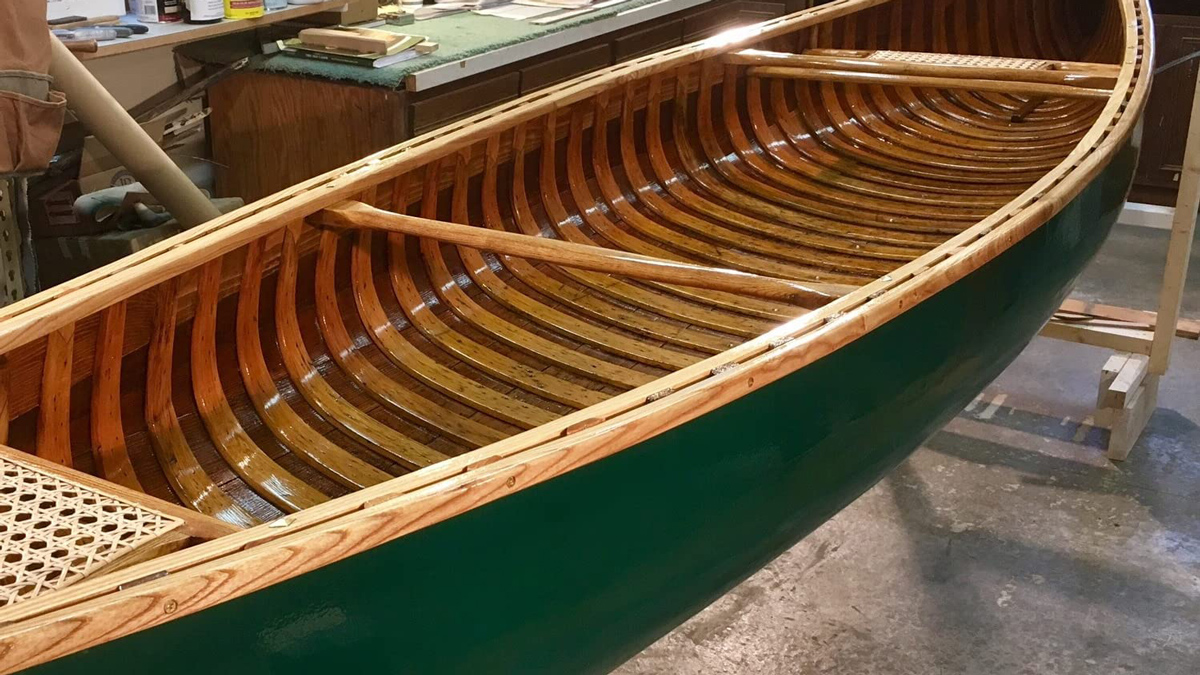
Best boat varnish: 7 top options for gleaming woodwork
Few things are as quintessential to the archetypal sailboat as gleaming, iridescent woodwork that is indicative of a recent coat…
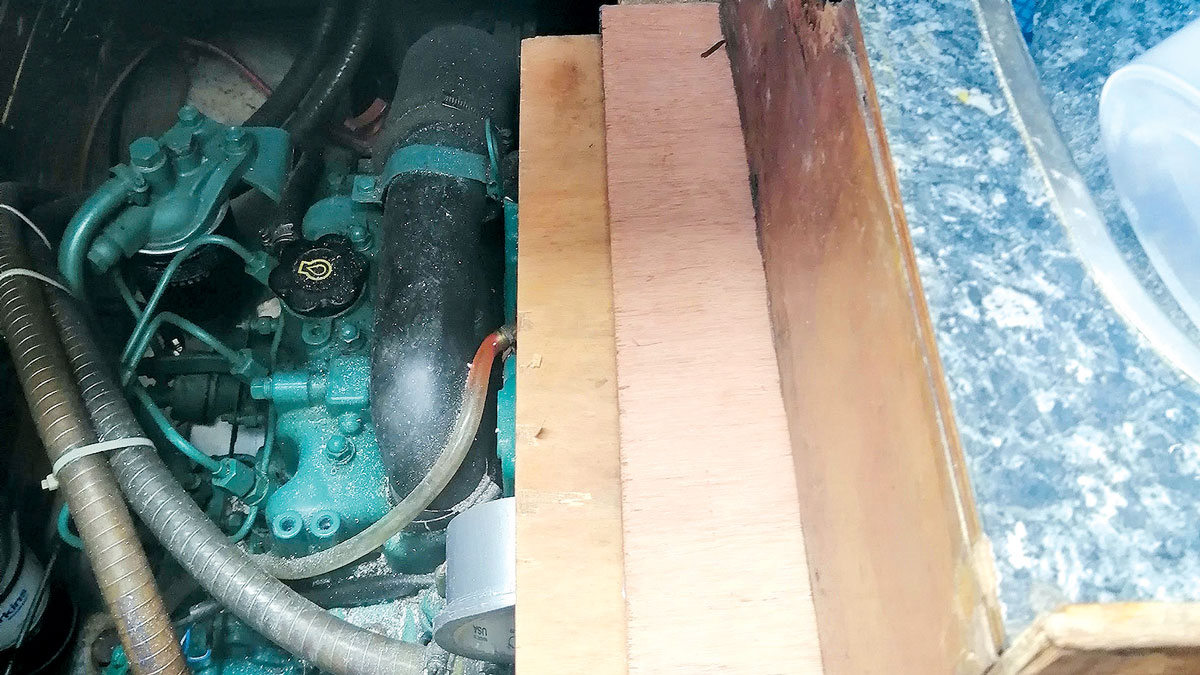
Replacing a rotten companionway step
James Wood gets to grips with epoxy when repairing a rotten step support on Maximus's companionway
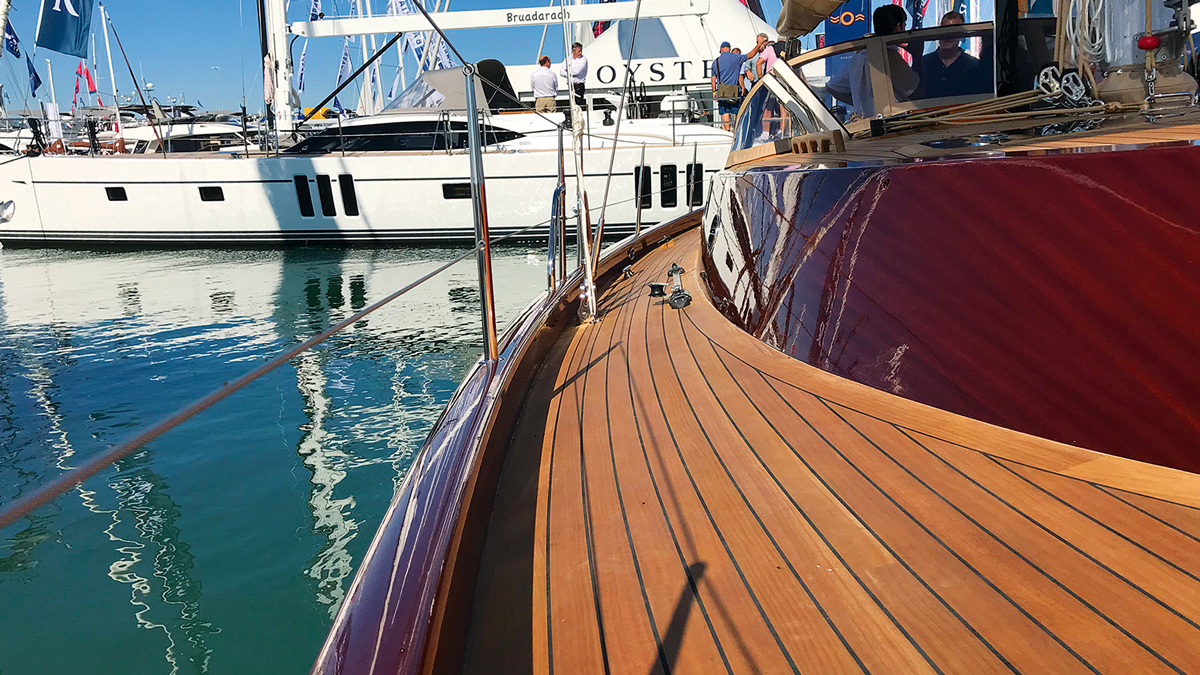
Teak alternatives: How to make your decks look as good as the real thing
However, according to a recent report by the Environment Investigation Agency, there are grave questions over the sustainability and sourcing…
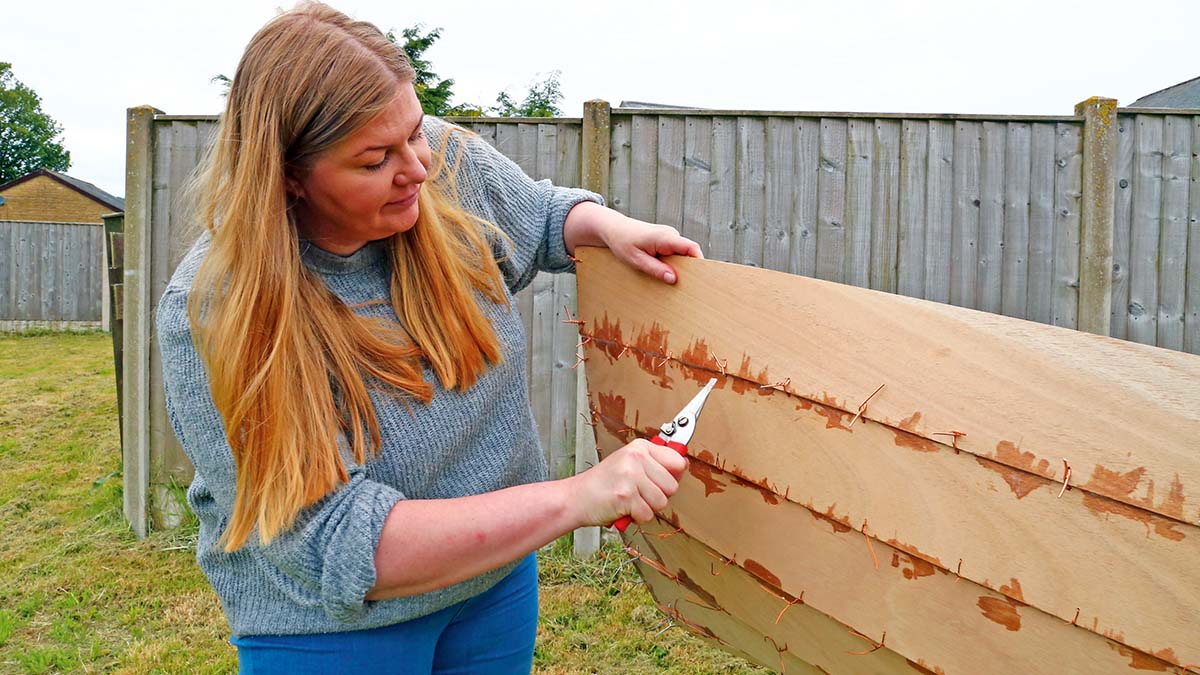
How to build a boat: Essential guide to building your first kit boat
You don’t have to be a boatbuilder to learn how to build a boat, argue Roger Nadin and Polly Robinson.…
While replacing the interior joinery, it’s worth thinking about how to reinvigorate the cabin and cockpit sole.
Of course, there’s nothing wrong with using a faced plywood subsole, but there might be an opportunity here to add a much harder and better-wearing cabin sole that is more appropriate for the rigours of life at sea.
Soles are often thinly veneered and satin vanished, which never seem to last past the first week of the season.
A more solid solution is beaded-edged Douglas fir or larch, which can look wonderful down below.
They can also be laid over a subfloor in your desired thickness and if you need it watertight, the beaded edge can be swapped for a caulked edge.
Allowing this to grey and develop a more natural look will not only reduce your maintenance but give you a harder-wearing, practical finish.
If you do end up dropping a bottle of red wine all can be fixed with some sandpaper and the process of time.
Best wood for masts
There is a section of the vessel often overlooked. We winterise our engines, boat covers go on and the cushions come ashore , then we think about our mast; ashore in the shed or utilised as a ridge pole, then stuck in the mast step or tabernacle for the rest of the season.
Owners of aluminium mast can fear not, but for anyone sporting a shiny wooden one it’s hardly unsurprising we often find some softer spots around the ends.
There is a lot to be said for the proper coating of spars but what do you do if your gaff, boom, or bowsprit is beyond repair?
Mostly our spars are made from softwood; on very unusual occasions, you might find a hardwood bumkin or bowsprit , but these are unusual.
When selecting timber for spars, the durability and structural integrity of the wood must be considered, but the most important factor is movement.
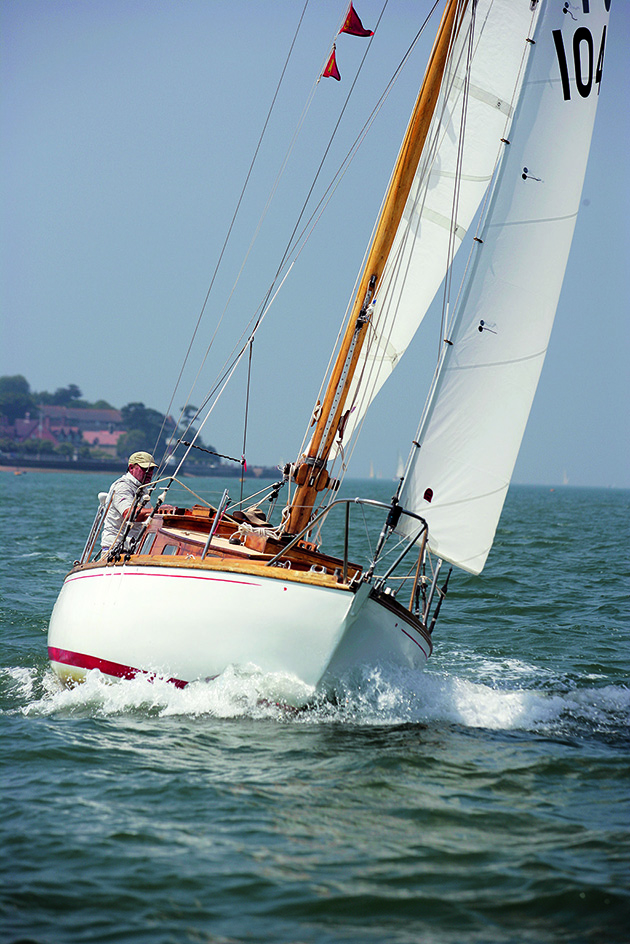
Wooden masts are generally made from softwoods, like larch, Douglas fir or sitka spruce. Credit Graham Snook/YM
Main masts, bowsprits and bumkins tend to require less twist and flex than gaffs , booms or the extremely endangered wooden spinnaker poles.
While I have seen smaller dinghies sporting oak, iroko and even ash for these spars, they’re not recommended unless you have a particular vessel requirement.
Larch is often used in larger working craft for these spars and if constructing a solid spar, this might actually turn out to be a good choice for a new home-crafted main mast.
As the availability of sitka spruce has dwindled and is now only available through very specialist suppliers such as Robbins Timber or Stones Boatyard, a discerning mast builder should look at Douglas fir, which gives movement, structural integrity and durability.
This solid wood is excellent for glued construction and is also easy to work with – important if this is your first foray into wooden mast building.
There is some lovely slow-grown, tight-grained timber on the market currently and it can be sourced in the UK.
Boat wood for strong steering
Fortunately or not, many boat owners will only have to varnish and care for their wooden tiller.
Again, there are plenty of options, but it is worth thinking about what you require – durability, integrity and movement – and also think about the aesthetics.
Iroko and oak are strong and durable and can stand the weather uncoated, whereas Douglas fir or mahogany tillers will need coating.

Ash is the preferred choice for a tiller – like on this Hallberg-Rassy 29 – as it’s strong and not too heavy
Unless you manage to find a grown shape in oak, all of the above will require laminating so the tiller doesn’t have lots of short grain which results in a weak construction.
Traditionally, tillers were always made of ash; this is a wonderful timber that is very strong but not too heavy, ideal for balancing transom-hung rudders .
However, ash is not readily available.
Whatever wood you use to build your tiller, it is a good idea to make a spare to store down below in case of an emergency.
Build solid
Timber selection isn’t just important for repairs and replacement, it also has huge implications for the construction of new wooden vessels.
As traditionally used timbers, such as grown oak and elm, have all but disappeared from the market, many traditional boatbuilders are now having to think far outside the box.
Centrelines were traditionally built in oak, but now iroko, opepe and even purple heart are all being used in its place.
These woods have proven longevity, having been used during the early restorations of classic boats which are still sailing regularly today.
For sawn and steamed timbers, oak is still the most popular.
Some builders are using the laminate construction of iroko or mahogany for building larger craft, but this tends to be for ring frame constructions and combines the deck beam into this process.
Carbon compatible
Companies such as Spirit Yachts have really pushed this a step further by combining carbon fibre alongside this timber construction; a great way to add strength to a boat.
Transoms, coamings and other brightwork still, for the time being, carry the trends seen over the centuries, with mahogany or teak being favoured, but this could change as the availability of timber changes.
Possibly, we will see more of a workboat look coming in, with these surfaces becoming painted and less exotic, but still durable.
The biggest challenge facing the modern boatbuilder is sourcing good quality timber for hull planking.
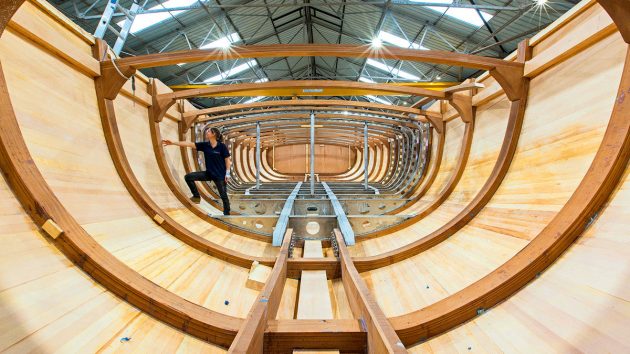
The centreline of the Spirit 111 was made using Douglas fir; a stainless steel space frame on the middle ring frames adds stiffness. Credit: Mike Bowden/Spirit Yachts
The wood needs to provide the length needed, without forcing lots of unnecessary scarfing planks and has to allow steaming and the twist of tricky underwater profiles.
The traditional boat scene soldiers on with oak and larch in this regard, and the vessels built at Working Sail in Cornwall show what can be achieved.
Other builders are using alternatives though.
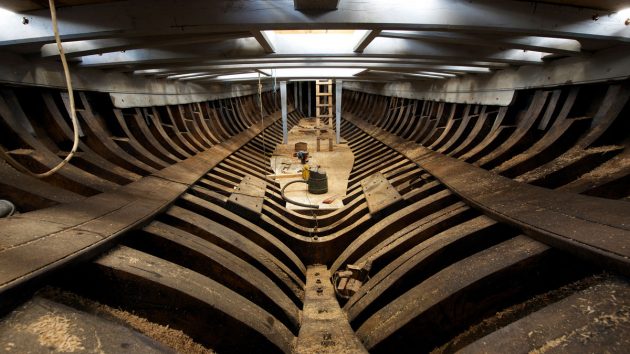
The Falmouth Pilot Cutter, Pellew , built by Working Sail, has oak frames and planking. Credit: James Stewart
Dan and Barry Tester rebuilt smack hulls from iroko, while Gerard Swift used Khaya mahogany to plank his skiff Mersea Native in 2000, which is still sailing today. If you can source larch, it’s a good middle ground between all of these options.
The reality of timber availability will soon catch up with us all, eventually limiting the options for amateurs and professionals alike.
In the meantime, however, if you remember the three golden rules and select a timber suited to your needs and requirements, you shouldn’t go too far wrong.
The best boat wood for the job
Centreline timbers.
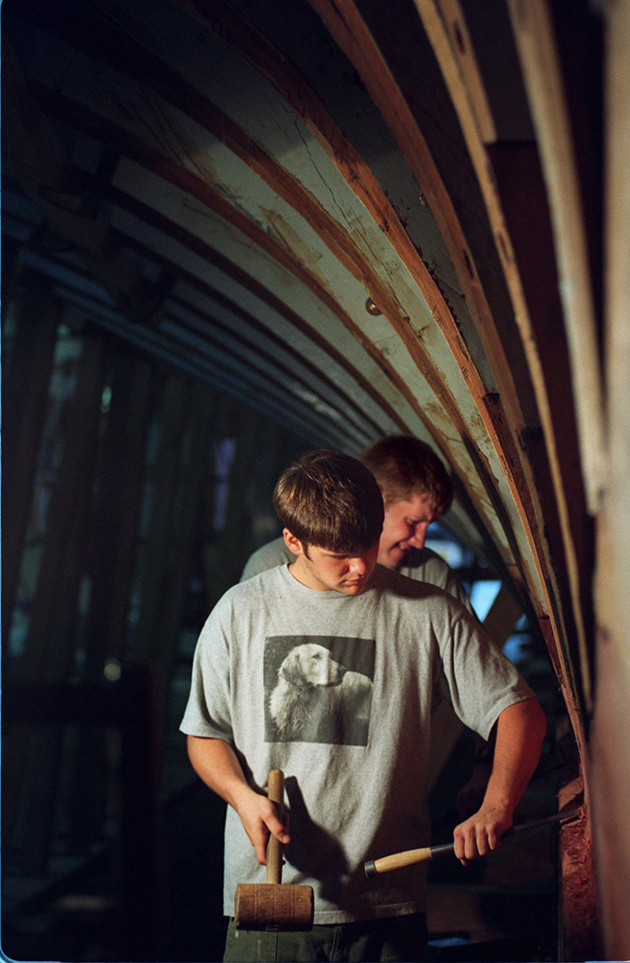
Purpleheart is durable, water-resistant and reacts well with changes in humidity, making it ideal for use in the centreline of a boat. Credit: Getty
The centreline of a vessel requires a timber that’s strong, durable and long lasting.
- Pros: strong traditional choice, often allowing the option of grown pieces with stem construction.
- Cons: lengths of long, clear timber are hard to find. Green timber is prone to movement as it seasons. Expensive.
- Pros: stable timber available in long lengths, often able to provide wide boards which is important when looking at constructing hogs. Represents relative value for money. Works well for lamination when creating curved stems or stern posts.
- Cons: often hit and miss in terms of quality.
- Pros: stable timber available in long lengths. Reasonably priced, heavy timber.
- Cons: can check heavily in sunshine; if working outside keep it covered or apply a priming coat. Can occasionally reject coatings and sealants, so it is worth researching which coatings are successful.
Purpleheart
- Pros: durable, insect and water-resistant. Purpleheart also reacts well to constant temperature and humidity changes.
- Cons: harder timber can be unkind to tools and tricky to work with.
Douglas fir
- Pros: long lengths of large, clear timber available, can provide great options when looking for sustainable-sourced timber. Much kinder on tools.
- Cons: not as durable as hardwood for a keel but not a bad choice for internal keelsons and deadwoods.

Most woods used for transoms – such as surian on this Balmain Bug, will need plenty of coats of varnish. Credit: Crosbie Lorimer
For those of us sporting neat canoe sterns or long sweeping counters, this isn’t much of a concern, but for others, transom timber choice is vital.
It’s also often required to take a coat or nine of varnish.
- Pros: beautiful varnished finish. Responds well to steaming and lamination. Long lasting and rot resistant.
- Cons: expensive and scarce.
- Pros: nice varnished finish. Responds well to steaming and lamination. Long lasting, wide-boards available.
- Cons: hit and miss in terms of quality. Often hard to purchase large quantities of colour matched boards.
- Pros: beautiful varnished finish. Responds well to steaming and lamination. Colour matched boards available.
- Cons: needs to be well cared for to ensure longevity.
Hardwood veneers
- Pros: various options for varnished finishes. Wide. Used with glues and hidden fastenings, it can provide stunning results.
- Cons: can be tricky to work with as easily damaged and requires thoughtful preparation before and during coatings. Needs to be placed on strong foundations.
Floors and frames
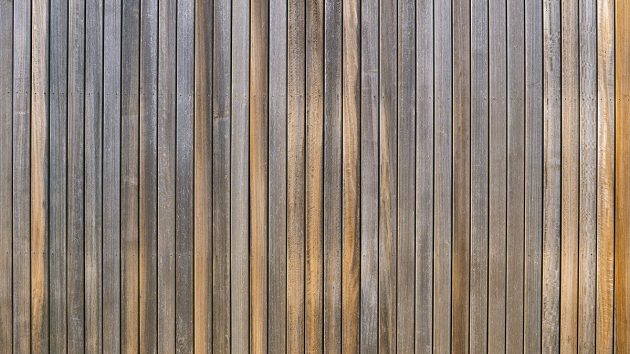
Iroko is ideal for lamination. Credit: Getty
An important structural element of any vessel, while many modern alternatives of carbon and laminate exist, the more traditional choices are limited.
It’s important to think about short grain when looking for curved pieces.
- Pros: the only single piece timber if you require any shape. Strong and reliable.
- Cons: expensive. Grown pieces are becoming harder to find.
- Pros: strong, good for lamination and steams well.
- Cons: grain short for curves.
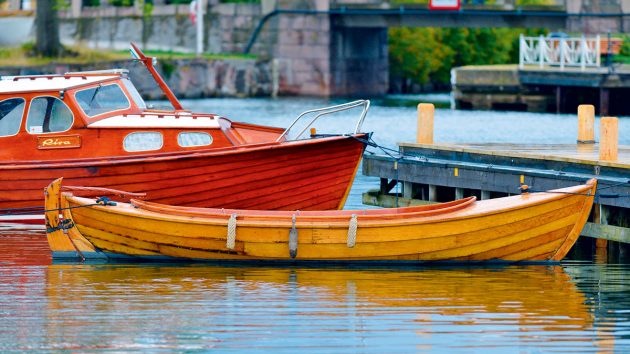
Oak bends and steams well, making it ideal for planking, although it is expensive to buy. Credit: Ilkka Ranta/Alamy Stock Photo
Choosing a suitable planking material is as important as it helps to determine the overall weight and strength of the vessel.
Consider what you want the planks to do: Are there tight curves? Lots of wear? Or is it all about grams of weight and dry sailing?
- Pros: a traditionalist’s choice when paired with oak. Available in long lengths. Strong and long lasting. Steams and bends well.
- Cons: wider boards becoming trickier to find. Beware of knots and sap and imitation pines.
- Pros: fantastic strong choice. Can be vanished as a topside finish. Steams and bends well. Wider boards available. Thicker boards can be cut to provide split planks and colour match for a varnished finish.
- Cons: prone to cracking or splitting when fitting or fixing. Check for rot and sap when purchasing wider boards.
- Pros: wonderful strong timber. Durable and rot resistant.
- Cons : limited on width of boards. Doesn’t bend or steam particularly easily, but can be done. Prone to checking and cracking under UV, even through coatings.
- Pros: strong and hard wearing. Steams well.
- Cons: can suffer becoming wet and dry, so needs one constant state – better being used below the water line. Hard to find outside of reclaimed stock.
- Pros: strong timber. Bends and steams well.
- Cons: can react to fastenings, and suffer UV damage.
- Pros: lightweight and easy to work with.
- Cons: lightweight timber, expensive and doesn’t last as long as other choices of timber.
- Pros: bends and steams well, making it perfect for awkward shapes.
- Cons: expensive. Difficult to source wide and long boards. Prefers to be in a constant state of temperature and humidity, so it is better used below the waterline.
- Pros: varnishes well for topside finish. Bends and stems well. Doesn’t react with fastenings.
- Cons: doesn’t always have the longevity of other timber. Doesn’t stand up well to freshwater damage.
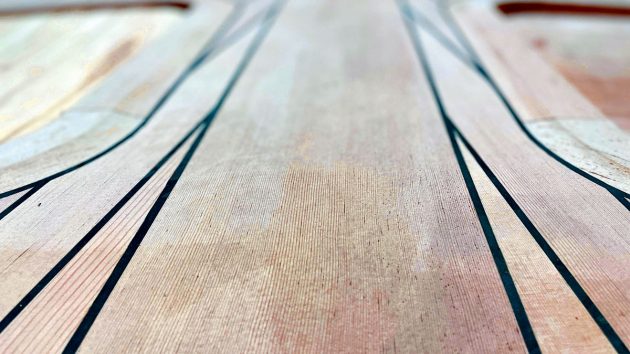
Boatbuilders, like Spirit Yachts, are now using Douglas fir for decking. Credit: Jessie Rogers
When choosing wood for decking, think not only about strength and waterproofing, but the overall looks and aesthetics it’ll bring.
- Pros: wonderful traditional choice that both weathers well and lasts. Works well over a subdeck. Solid planks.
- Cons: don’t over-scrub and wash with a brush. Expensive and harder to find.
- Pros: great alternative to teak. Works well over a subdeck. Solid planks. Wide boards are available.
- Cons: doesn’t last as long as teak. Not as soft under barefoot. When machining large amounts and creating dust, it is highly toxic.
- Pros: cheaper alternative to hardwood. Weathers to a beautiful silver. Lays well over a subfloor and solid planks.
- Cons: soft and can be easily damaged.
Rubbing strakes and toe rails
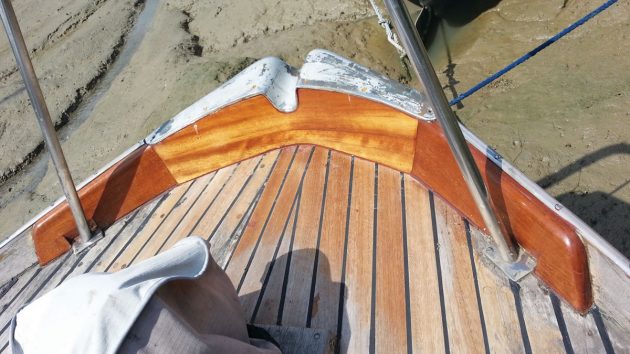
Hardwood, like teak, is best for toe rails. Credit: Mike Taylor
This is a high impact area, rarely varnished and undercoated. If you can, look for a hardwood option here.
- Pros: hard wearing and weathers well. Rot resistant.
- Cons: expensive, hard to find.
- Pros: great alternative to teak. Wide boards available which is handy for tall toe rails.
- Cons: can be tricky to steam small section round bends. Highly toxic.
- Pros: varnishes well for topside finish. Bends and stems well. Doesn’t react with fastenings. Ages wonderfully under varnish layers.
- Cons: doesn’t stand up well to freshwater damage.
- Pros: strong timber. Bends and steams well. Looks better when scaled up in large sizes.
- Cons: can react to fastenings, and can suffer UV damage. Expensive choice. Can reject vanishes and expoxies.
- Pros: cheaper alternative to hardwood. Weathers to a beautiful silver colour.
- Cons: soft and easily damaged. Can soak up the varnish coats.
Cockpit gratings
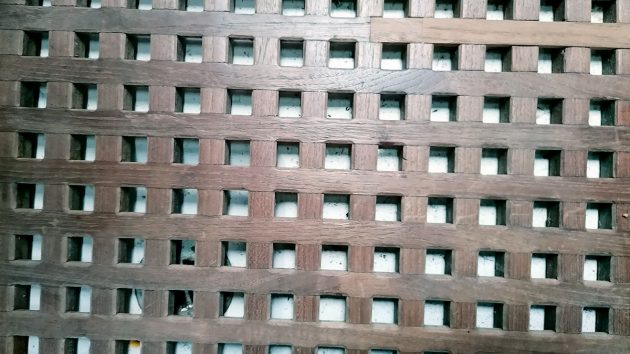
Teak is highly rot resistant, making it ideal for a cockpit grate . Credit: Katy Stickland
- Pros: hard wearing, and weathers well. Highly rot resistant.
- Pros: great alternative to teak.
- Cons: doesn’t last as long as teak. Not as soft under barefoot. Toxic when machining large amounts.
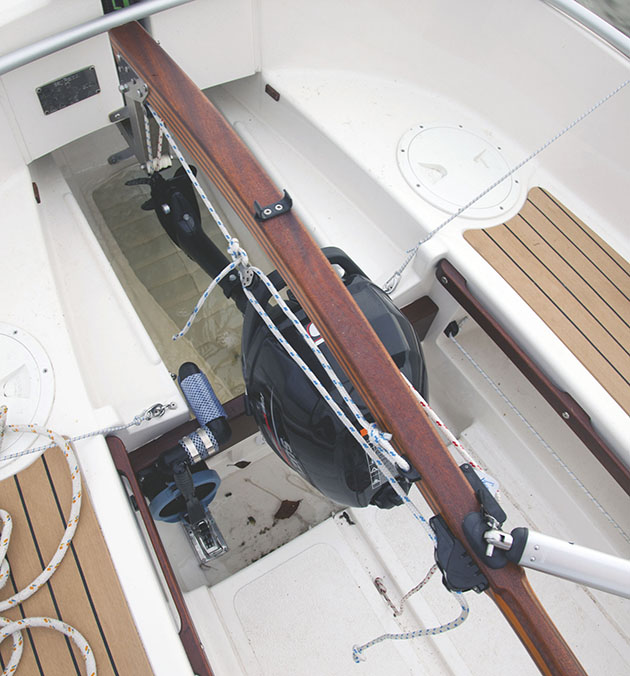
Douglas fir is lightweight. Here, it has been mixed with utile on the tiller of this BayRaider Expedition to give it added strength and to accommodate the curve over the head of the outboard engine. Credit: David Harding
- Pros: strong, curved pieces available to avoid short grain.
- Cons: goes black when uncoated. Not very rot resistant. Reacts to fastenings.
- Pros: strong timber. Laminates and steams well.
- Cons: short grain for curved areas
- Pros: strong. Grown pieces so good for curves.
- Cons: costly. Avoid green wood.
- Pros: lightweight timber. Laminates and steams well.
- Cons: Goes black when uncoated. Not very rot resistant.
Enjoyed reading Boat wood: a complete guide for yacht owners?
A subscription to Practical Boat Owner magazine costs around 40% less than the cover price .
Print and digital editions are available through Magazines Direct – where you can also find the latest deals .
PBO is packed with information to help you get the most from boat ownership – whether sail or power.
- Take your DIY skills to the next level with trusted advice on boat maintenance and repairs
- Impartial in-depth gear reviews
- Practical cruising tips for making the most of your time afloat
Follow us on Facebook , Instagram and Twitter
6 Best Boat Wood For Boat Building

Do you want to build a wooden boat from scratch?
Buying a boat is easier, but building one will give you even greater satisfaction. Whether you are looking for a challenging weekend DIY project or you want to put your handy skills to use in building something practical, boat building is a perfect choice.
The most crucial part of this project is selecting the right wood. This can be confusing as there are many types of wood for boat building. What’s more, depending on the type of boat , you might need different types of woods for the different parts.
If you want to find the best boat wood for boat building, you have come to the right place! As someone who has built several boats, I am happy to share what I have learned about selecting the right lumber for a DIY boat .
So, without further ado, let’s look at the best boat-building woods .
Best Boat Wood For Boat Building

Spruce is one of the best boat woods for boat building . It is a softwood but strong and durable, making it ideal for building boats.
As a softwood, working with spruce is comparably easier as the wood is bendable and easy to cut. But, you should ensure that the spruce lumber you choose is knot-free and of high quality.
Spruce glues together well, making it a good choice for someone building a boat for the first time. This wood also stains and finishes well, so you can easily apply wood finisher and paint to your boat to protect it from the effects of UV rays and moisture.
The excellent strength-to-weight ratio is another quality that makes spruce wood a good choice for boat building. Good strength to weight ratio means the wood bends easily, but it is strong enough not to break. While it is strong, it is also light enough to carry, cut, and build with.
- Easy to work with using small and large tools
- Glues well and holds finish and paint
- Good strength to weight ratio
- Durable and low maintenance
- It needs to be well-stained and finished to prevent rot and fungi

Cedarwood is popular for its aroma, attractive color, and workability. There are different types of cedar, including red, white, Alaskan yellow, Atlantic white, Lebanon, Port Orford, Cyprian, Spanish and many more.
The three types of cedarwood best suited for boat making are red, yellow, and Lebanese cedar. Red cedar has an attractive color and would add to your boat’s aesthetic appeal. Yellow cedar is quite hard, making it durable and resistant to rot. Lebanese cedar has long straight grains, a sign of high-quality wood.
Cedarwood, in general, has many other great qualities that make it a top wood for boat building . Red cedar, for example, is lightweight and easy to cut and build with. It also contains a good amount of moisture, making it less prone to warping and breaking.
Most cedars are easy to work with as they are easy to cut and bend. It is also easy to drive nails and screws through the wood, and the surface lends itself well to paint, polish and glue.
Cedarwood is resistant to the effects of UV-rays, an important characteristic to consider when building a boat. The wood also contains chemicals that protect against insects and rot.
If well maintained, a boat made out of cedar can serve you for years.
- Rich, dark red color gives it an attractive appearance
- Resistant to fungi and insects
- Temperature and moisture resistant
- Durable but soft enough to cut and carve
- Finishes well
- Requires regular maintenance
- It can be dented easily due to its softness

There are more than 500 varieties of oak wood. Oak is incredibly strong wood and is chosen in marine applications for its straight and tight grain, coarse texture, durability, and low maintenance .
Compared to other wood for boat building, oak wood has a high density, making it resistant to fungi and rot. Many years ago, oak was the wood of choice for shipbuilding due to its durability in water and resistance to the effects of moisture.
Due to its straight and tightly packed wood grains, oak is easy to cut and scarf. It also lends itself well to gluing, staining, polishing, and painting, important qualities when building a boat. Like cedar, oak is also fire resistant, making it a safe wood for boat building.
- Very strong and durable wood
- Resistant to rot and fungi
- Durable in water and is ideal for marine application
- Easy to cut, bend, glue, stain, polish and paint
- Heavyweight can make it difficult to handle alone
- Presence of tannic acid can cause nails and screws to rust with time
4. Chestnut

Chestnut is a hardwood species but is surprisingly easy to work with; due to its user-friendliness, I recommend starting with chestnut wood for your first boat building project . In particular, sweet chestnut has excellent workability and is a great wood option for beginners.
The workability of chestnut wood can be attributed to its straight grain and minimum hardness. This makes the wood easy to cut, carve, and drill into, taking much of the hassle out of your boat building project.
Something else that makes chestnut such an attractive wood for boat building is its deep and rich brown color. Chestnut is a great option if you want a country, rustic appearance for your watercraft. Light-colored chestnut can be easily stained to enhance its aesthetic value.
That said, chestnut does split easily, and you should be careful when cutting along the grains to avoid unintentionally breaking your wood planks.
- Rich, beautiful rustic appearance and color
- Easy to use for beginners
- Straight grain wood and medium softness improves the wood’s workability
- Splits easily, and extra care should be taken when working with the wood
5. Ash Wood

Some species commonly used in boat-making are White Ash Wood, Black Ash Wood, and Green Ash Wood.
Ashwood comes in a light brown color and straight grains, making it an attractive wood for making a boat. Some species commonly used in boat-making are green, white, and black ash wood.
This wood is dense with medium softness; it bends and cuts easily, accepts nails and screws with ease, and finishes well.
When it comes to maintenance, Ashwood is quite easy to care for compared to other types of hardwood. The low maintenance and affordability make this among the best wood for boat building .
- Widely available and among the most affordable hardwoods
- Highly durable and requires little maintenance
- Easy to work with- it cuts and bends with ease and quickly accepts screws and nails
- Attractive with its light-brown hue and straight wood grain
- Wraps, when exposed to moisture so proper storage, is required
- Splits easily; you should pre-drill the wood before inserting screws or nails
6. Mahogany

Mahogany is the best wood for any woodworking project. If you are looking for quality and longevity, mahogany certainly tops the list. It might not be the cheapest or most accessible, but mahogany’s durability, workability, and beauty pay for themselves.
African, Cuban, Honduran, and South American mahogany is the species most commonly used for boat building. With little maintenance, mahogany can last up to 40 years even when exposed to water, soil, and UV rays.
With its strong water-resistant properties, you don’t have to worry about rot when you build your boat using mahogany wood. It also doesn’t shrink or warp with changes in weather, which is usually a major concern with wooden boats.
Despite being a hardwood, mahogany is easy to work with using small and large hand tools. It easily accepts screws and nails and holds paint and polish very well, which further helps to protect your boat from the elements.
Lastly, mahogany has a rich, uniform color that gives your boat a really attractive finish.
- It has a rich, attractive color and straight wood grain
- Strong but easy to work with using small and big hand tools
- Resistant to rot and weather elements
- Low maintenance and can remain in good shape for 40+ years
- The wood is quite heavy, and you may need an extra hand to help you handle a large log
- Mahogany is in high demand, and its availability has decreased with time, making it rare and expensive
Summary: 6 Boat Wood for Boat Building
Building your own boat can be an exciting project and a way to put your woodworking skills to great use. Workmanship is as important as choosing the right wood for the job. There are many different boat wood for boat building, all with excellent qualities. In the end, your choice will depend on the wood’s availability, cost, level of workability, and, of course, the aesthetics you are looking for. Good luck with your boat-building project!
Related posts:
- 5 Types of Marine Heads: Which is Better?
- Kelly Blue Book Boat Values (3 Types)
- 4 Simple Steps to Paint A Fiberglass Boat
- 8 Typical Boat Steering Problems (Fix Tips)
2 thoughts on “6 Best Boat Wood For Boat Building”
thank you for the info! I plan to bild one
That was so very helpful! I’d love to build a Viking longship but a mini version. Any guidance would be terrific and appreciated!
Leave a Comment Cancel reply
Save my name, email, and website in this browser for the next time I comment.
Refastening a Wooden Hull - Season 4, Episode 1 Now Available!
Wood Selection: Choosing Boat Lumber
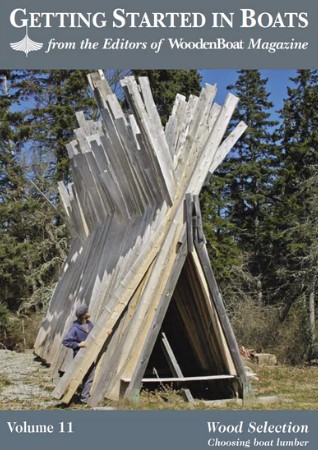
The original print version of this quide can be viewed as a PDF or purchased from the WoodenBoat Store.
W ooden boat building is different from any other form of woodworking. It requires curves and angles rarely found in furniture and house construction. Boats are structures that move. Because a boat spends much of its life in water, the wood used to build it must have certain properties that give it sufficient strength, make it resistant to rot, and provide resiliency when used in conjunction with fastenings, adhesives, and day-to-day use. So, as you begin to look at boatbuilding wood, there are certain things you’ll need to know.
In this issue of Getting Started, we’ll examine important characteristics of wood, look at some of the wood species and plywood types used in boatbuilding, and give you some pointers on how to create a stock list. This article is limited to wood selection, so you won’t see processes such as milling, machining, or working wood covered here. This overview, we hope, will help you select the best material for your project and help you to get the most out of every board foot.
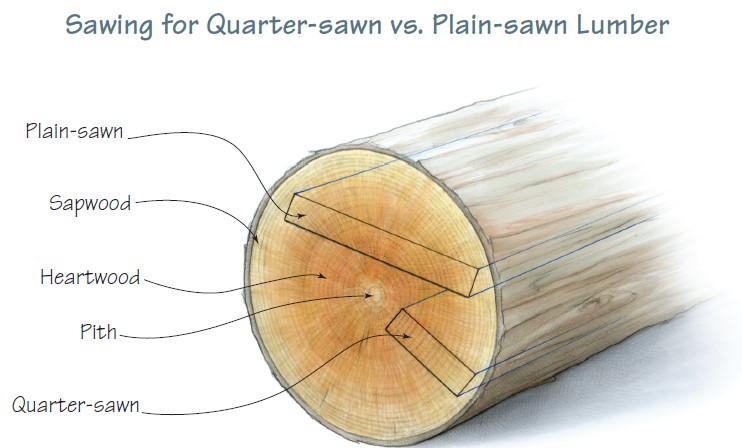
Wood Basics
W hen selecting wood, it’s important to consider dimensional stability. Dimensional stability refers to how much a board shrinks or swells. One way that sawyers can help assure some level of dimensional stability is by taking cuts in the log that best utilize its growth-ring pattern for minimizing shrinkage and swelling.
What to Look for in Boat Lumber
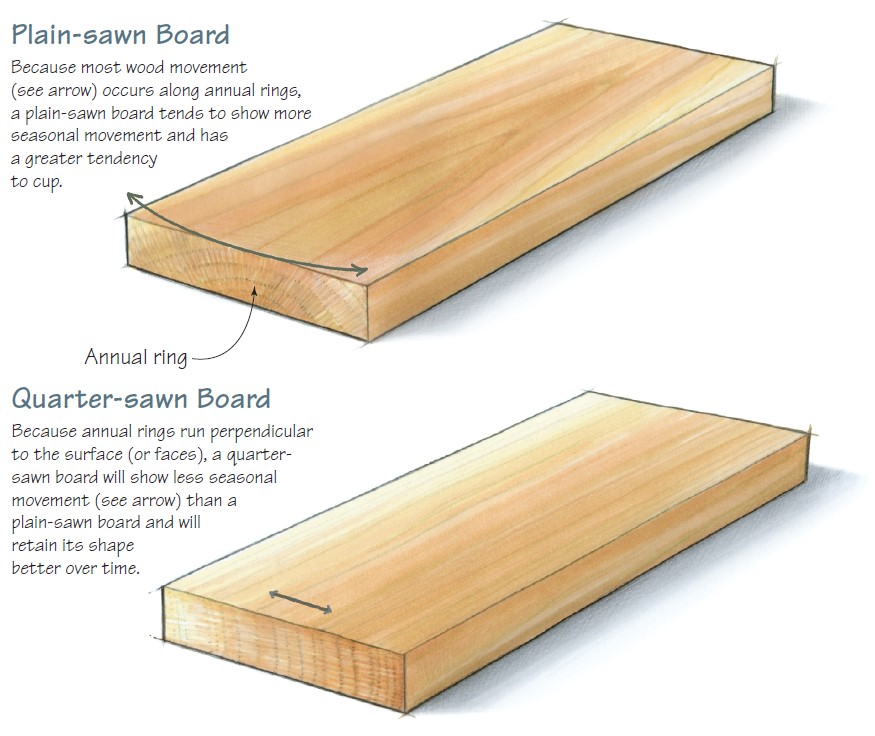
Quarter-sawn lumber will have good dimensional stability across its face. It is usually considered the prime cut and, as such, costs more than the other cuts. Plain-sawn (or flatsawn) wood will have a tendency to cup and, over time, it will appear as if growth rings are trying to flatten out. Quarter-sawn wood is good to have in some boatbuilding applications, such as planking below the waterline, where swings in shrinkage and swelling are greater than they are on the remainder of the hull. Plain-sawn wood is suitable for planking and other components in small boats. Heartwood (the older part of the tree) is often more durable than sapwood (the outer rings in the living tree). Sapwood of any species is considered non-durable. Some boatbuilders shy away from using sapwood, others do not. Personally, I am less inclined to use it unless I can place it well above the waterline.
More Terminology
H ere are some characteristics and terms commonly used when dealing with boatbuilding lumber; the first four have to do with warping.
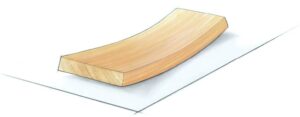
Bow—Curve along the face of a board from end to end, like a rocker at the base of a rocking chair.
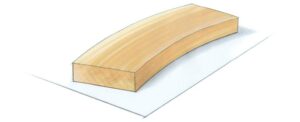
Crook—The end-to-end curve (warp) along a board’s edge. Not to be confused with this form of warp is the term crook timber, also known as compass timber (and often referred to as “a crook”), which is sawn from the roots and branch crotches of trees. The natural curvature of crook timber makes strong and beautiful stems, breasthooks, and quarter knees.
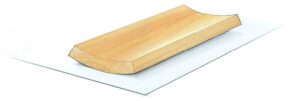
Cup or Cupping—Curve along the width of a board from side to side. Cupping is the result of uneven drying. Using even slightly cupped wood on a table saw heightens the danger of the operation because it can lead to a pinched blade and kick-back. If cupped wood must be used, I favor cutting with a bandsaw, as it is less likely to cause harm. When cutting cupped wood on a bandsaw, be sure to place the board cupped-side-down on the worktable (as a frown) for better stability while you work.
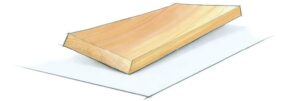
Twist—An uneven warping that makes the board appear to be spiraling. This defect is a dangerous one to mill, a difficult one to correct, and should be avoided if possible.
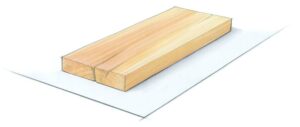
Checks or Checking—Cracks in the wood, usually found at board ends and sometimes found in the middle of the board. Checking can be a result of uneven drying, living tree shakes, or mishandling (dropping). Look carefully at boards that have checks. While checks may appear to be only a few inches long (and many are), they might indicate a major weakness along the board’s length.
Pitch Pocket—A pitch pocket is an opening between the growth rings that now holds, or did hold, resin.
Live Knot— Live knots (also known as tight or red knots) are so named because they were alive when the tree was harvested. They are more firmly attached to the board than dead knots. Since they usually are not rotten, they can sometimes be left alone rather than drilled out and plugged.
Dead Knot, Loose Knot, Black Knot— Dead, loose, or black knots are from a branch that was dead at the time of harvest. These are dark, rotten, and usually loose or easy to loosen and should be removed. They’ll leave a dark hole that should be reamed free of residue and then plugged.
Four-quarter (4/4)—A way of describing stock according to the number of “quarters” or quarter-inches in its thickness. Boards that are 1″ thick are referred to as four-quarter (4/4) stock. Five-quarter (5/4) stock is 11⁄4″ thick; six-quarter (6/4) stock is 1 1⁄2″ thick; eight-quarter (8/4) lumber is 2″ thick. Expect these to be rough-sawn dimensions, especially if wood is purchased from a lumberyard. Finished wood denoted as 4/4 will actually be somewhat thinner than an inch. So, if you need wood that is truly 1″ thick, you’ll need to buy rough stock that is 5/4.
Rough or Rough-sawn Lumber—Wood that has not yet been planed to finished thickness.
Finished Thickness—Wood that has been planed to its final thickness and is ready for the project at hand.
Wood Species
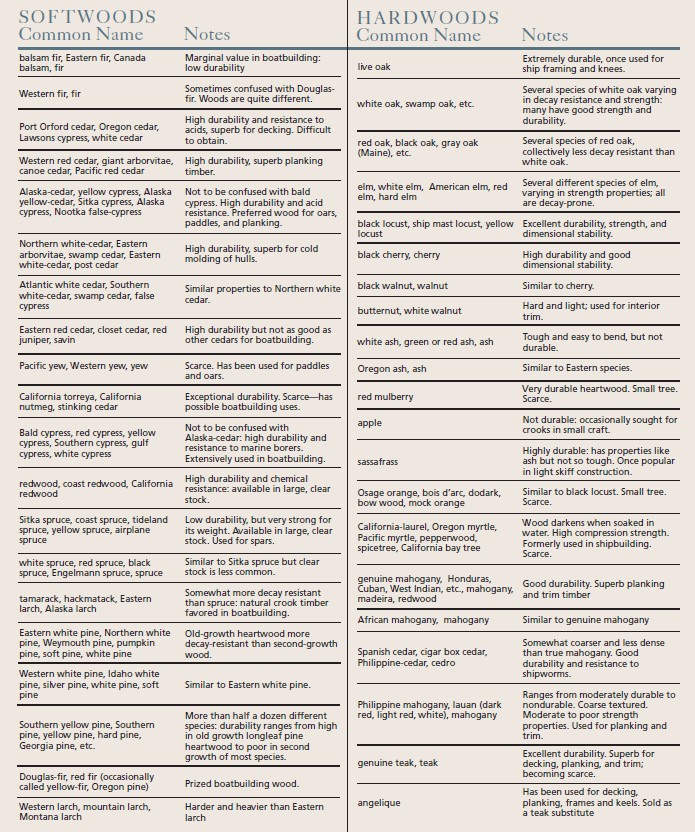
D r. Richard Jagels, professor of forest biology at the University of Maine in Orono and a regular contributor to WoodenBoat , prepared the following list of wood species that are often used in boatbuilding. It should be noted that the advent of strip-building has opened new frontiers to small-boat builders. Often used to construct canoes and kayaks, this process usually includes gluing together long, thin strips of wood on a mold into a hull shape and then encapsulating it with fiberglass cloth and epoxy. Woods such as walnut, basswood, and a variety of other species that are not traditionally thought of as boatbuilding (or at least hull-building) woods are now regularly used for strip-planking. They offer new options and color choices for small-boat construction.
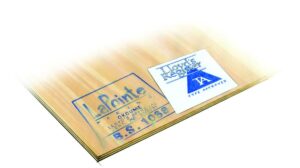
P lywood continues to gain in popularity among boatbuilders, especially those who build small boats. Chief among the reasons are its dimensional stability and its availability. It is also becoming increasingly difficult to find natural wood that is wide enough for some planking. For example, in building a traditional skiff, it is not uncommon to need a 14″ – wide board for the garboard (lowermost) strake. Also, plywood is more split-resistant, often outperforming even a properly steamed natural plank.
Some plywood is not suitable for use in a marine environment. To assure that yours is, you’ll need to look at its rating.
One basic classification to look for is B.S. 1088. The B.S. stands for “British Standard”—an acknowledged standard-setting entity. The “1088” is their best-known designation for marine plywood that is suitable for small-boat and pleasure-boat building. It is manufactured with waterproof glue and has a very limited number of small voids. An additional assurance that your plywood meets these standards comes from Lloyd’s Register. The Lloyd’s sticker on the sheet indicates that, in addition to meeting the British Standard, the manufacturers have placed themselves under the scrutiny of Lloyd’s and have agreed to meet with their standards. B.S. 1088 with the Lloyd’s sticker is more costly than the rest—but many builders feel that it’s worth it. When you consider how little the cost of materials is in the scheme of building a boat (time in labor is the greatest expense), I would agree with them. When you shop for plywood, make sure that it meets B.S. 1088 or a comparable standard.
Another factor to consider is the boat’s intended use. Our technical projects manager and resident boatbuilder here at WoodenBoat, Tom Hill, says, “When I build a small boat that needs to be lightweight but can be stored in a garage, I use okoume. It is easy to work and it takes paint well. When weight is less of a concern and I need the boat to be highly rot and abrasion resistant, like when I’m building for an owner who plans to moor his boat all season, then I’ll use sapele.”
When looking for marine plywood, it’s important to ask questions. Reputable dealers will help you, even if you don’t wind up buying from them. To learn more about marine plywood, I encourage you to read Chris Kulczycki’s article on the subject in WB No. 174.
Calculating Board Footage
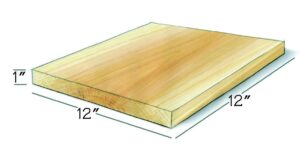
B oard feet” is a way to express lumber volume. One board foot is equal to 144 cubic inches of wood. To find board footage of an amount of wood, we multiply the thickness (in inches) x the width (in inches) x the length (in inches) and divide it by 144 .
So, for our 1 BF we have: 1″ x 12″ x 12″ = 144 cubic inches 144 cubic inches /144 = 1 BF
Now let’s look at a more complex scenario. Here we have a board that is 2″ thick x 12″ wide x 8′ long. First, let’s convert the length measurement into inches. Now we have: 2″ x 12″ x (8′ x 12″ [per foot]) = 2,304 cubic inches then 2, 304 cubic inches /144 = 16 BF
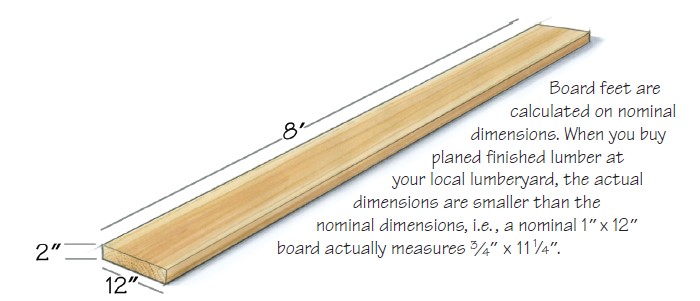
Making a Stock List
W hether you plan to purchase your wood or go out and harvest it yourself, it’s a good idea to begin your planning by making a stock list (aka: cut list). It may take some time, but in the long run having an accurate stock list will be a big help in estimating costs, and it will guide you in your selection of stock.
The chart has spaces for the individual pieces, the number of pieces needed, their finished dimensions, rough dimensions, wood type (species or plywood type), comments (such as notes or sources), and board feet (BF). You can easily make a chart by hand or on your computer, or you can download one from our web site <www. woodenboat.com> (click on “Getting Started in Boats”).
Begin by looking at your plan. List the names of each piece in the stock list. Some people like to list items according to their building sequence. I prefer to list them according to wood species used. Then, put in the finished dimensions of each piece. Depending upon the level of detail given in your plan, you may need to do some “guesstimating.”
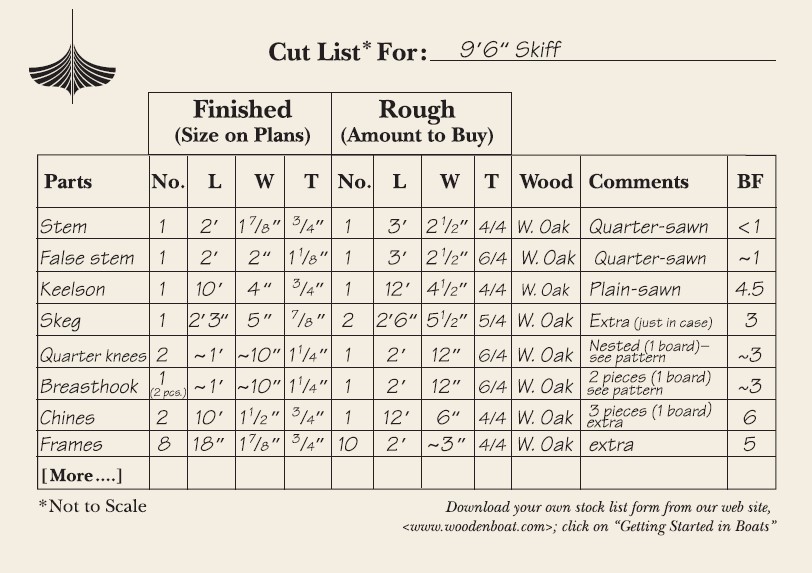
Details such as finished plank lengths can be difficult to pick up from the plan since they are either foreshortened or don’t go in a straight line in every view. Planking presents other special challenges, too. The forward part of the plank may be wider than the aft section. This is often the case with the garboard plank on a traditional skiff. This type of plank may be built out of two boards of different widths. If you choose to do this, make a note of it on the stock list and account for the added length that will be needed to join the two boards together with a scarf joint (a long, tapered joint between two long pieces of wood). Once you have determined the overall finished lengths of your planks and plank pieces, add two to three feet to the overall hull length (rough dimensions) to allow for bending and clamping. Do the same for other long components.
Also note which pieces, such as quarter knees, can be nested (almost like interlocking pieces) or configured around a knot and cut from the same board. I find it helpful to make a sketch of how these could be laid out and what type of board and grain pattern is best.
Finally, in tallying your stock list, you’ll need to add extra BF to account for waste and defects. Are you sitting down? For planking, especially if your stock is live-edged (with the bark still on it), has sapwood, and a lot of defects, plan on over-buying by as much as 100%. For other pieces, plan on buying 30–50% more wood than you think you’ll need.
Locating and Storing Wood
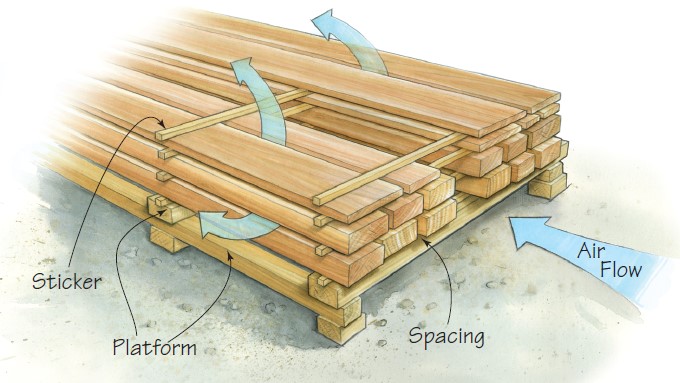
Locating wood—Finding wood for boatbuilding can be a challenge, especially for people who live far from where it is harvested. Unlike the species needed for house construction or furniture making, boatbuilding woods are rarely carried by lumberyards. Get to know a local sawyer, if possible. Lumberyards and big-box stores can be a good place to buy interior or exterior grade plywood (non-marine use), or medium- density fiberboard (MDF) for building jigs and molds. Occasionally, you can even find wood for components like thwarts.
Finally, I’d be remiss if I didn’t mention that one excellent source for locating boatbuilding wood and specialty lumberyards is the classified ad section of the magazine you are now reading.
Storage—The cover photograph for this issue of Getting Started shows how we store white cedar planking stock at WoodenBoat School here in Brooklin. This idea came to us from Harry Bryan, a popular instructor at the WoodenBoat School and a contributing editor to this magazine. While a practical and ingenious idea, most people don’t have the room or the need for this much lumber. The illustration above depicts a method that will work for just about anyone.
Distribute your lumber by weight. Place the largest, thickest pieces at the bottom of the stack. Don’t forget to place stickers under the bottom-most pieces. Make sure that there is at least a finger’s-worth of space between boards that are placed next to one another. Follow this procedure as you place each (progressively lighter) layer of wood on the stack.
Whether your wood is home-harvested or an online purchase, the quest to find boatbuilding lumber shouldn’t feel like a trip to the woodshed. We hope that we have provided you with some new insights so that you’ll know what to look for (and look out for) when selecting wood for your next project.
Karen Wales is associate editor of WoodenBoat. She thanks Dick Jagels for his contributions to this article.
Further reading: Considered the preeminent source in the United States, “Wood Handbook: Wood as an Engineering Material” from the USDA Forest Products Laboratory in Madison, Wisconsin.
Building an Amesbury Skiff – Part 1
Varnishing basics, marine plywood – a consumers guide, subscribe for full access.
Flipbooks are available to paid subscribers only. Subscribe now or log in for access.
Welcome to
Bristol , s hipwrights.
It's been 10 long months since the last episode of Building Evelyn. But there's a new one that picks up where Lou and Ken left off. We're updating the website. Check out the new Gallery photos and video. And we're scheduled to post a new video on the first Friday of every month.
Watch Episode 18: Fitting, glueing and fastening planks.
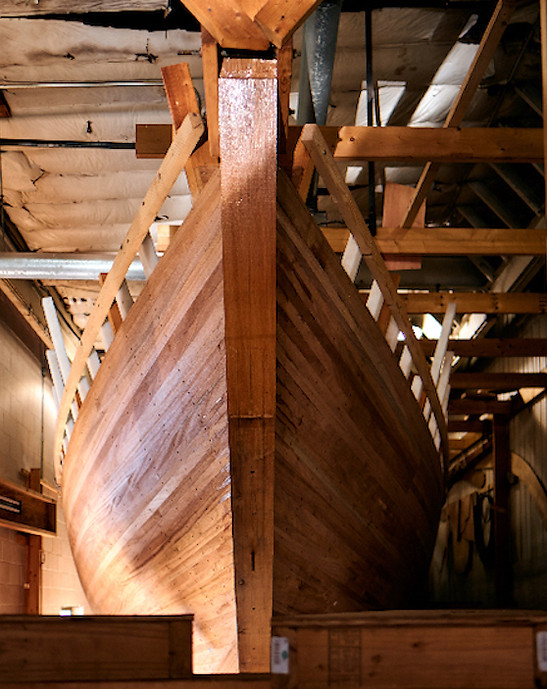
Our Mission
Bristol Shipwrights' mission is to preserve and demonstrate traditional woodworking and boat building skills and techniques. More than that, we're working to develop new ways to use the latest tools and materials to help us and you build stronger, more affordable and enduring boats and construction projects of all kinds. The best way we know to do that is to video and share with you our current and future projects. Evelyn is our first project and only the beginning. But we hope you'll join us for each and every video and voyage.
Meet Evelyn
Rethinking a cruising schooner from the 1920s

43” o.a x 33” w.l. x 12’ beam x 6’ 5” draft
Able offshore — handy — roomy, full keel schooner, ready for delivery, alden design no. 270.
Join Bristol Shipwrights as we document and video the challenges of building a 43' Alden 270 schooner. Whether you're a professional or backyard boatbuilder, a woodworker, or a dreamer, we're confident you'll learn something new about boats and woodwork from our screw ups and successes.
See the progress we're making on Evelyn

In EP17, pretty much the whole crew worked seamlessly to glue up Evelyn's heavy deck beams. All beams were made from the strip planking off-cuts.

The simplest way to make a pattern for a plank requires a stop at the lumberyard and the office supply store. See how in EP16 of Building Evelyn.

Best Wood for Boats: Finding What Works for You
Availability, size and cost, ease of use, elemental resistance, classic appeal, easy to work, myboatplans: how to find the perfect wood, final thoughts.
To make sure that your boat lasts for many years of use, you need to make sure that you use the best wood for boats .
Every boat enthusiast has their preferences for boat building materials, but there’s no arguing that some are simply better than others.
Top resources, such as MyBoatPlans, can help you to find the right wood types for different areas of your watercraft.
Considerations to Keep in Mind
There’s more to choosing wood than settling with certain varieties that are recommended by the professionals.
You’ll first need to make sure that certain wood types are available in your area. Otherwise, you’ll be faced with several excessive shipping and handling costs.
Some types of wood might need to be imported from different states or countries, tripling your costs.
You might also find that certain woods can work just as well as your top choice and are available to be sourced locally.
It’s a great idea to make a list of your top varieties and then rank them based on how easy they are to find.
Another essential factor to consider is whether your desired wood comes in the right size.
Certain woods can only be purchased in individual widths and lengths, making them ideal for a specific placement.
For example, the wood used in your cabin might not be large enough for the ribs.
If you need wood cut to specific sizes, you can guarantee it will also increase your coat.
Often, it can be better to opt for certain types of wood specifically meant for trim, flooring, ribbing, and more.
Once you get more experience with boat building, you can be a little more flexible with the wood you choose.
Some materials might be more challenging to work with than others in terms of holding nails, bending, or strength.
You might even find that you’ll need special equipment for certain varieties than others, which can be challenging to find for beginners.
Best Woods for Boat Building
There are more than enough wood options out there that are perfect for boat building. Among the most used are the following:
This wood is one of the easiest to source in North America, especially in the United States.
Another advantage of cedar is that there are several different kinds to consider, which are all easy to work with.
You can find them in longer lengths, with knots, or in grain-free designs. You can even find different cedar types with predrilled holes so that you won’t have to worry about splitting.
Because fracturing is one of the main disadvantages to cedar, it’s something to take into consideration.
Western Red Cedar
This cedar type has lesser tensile strength than the other types, which means it’s excellent for bending.
You wouldn’t typically consider using it for planking, but it can be phenomenal for small boats combined with fiberglass.
Another benefit is that western red cedar is often used for decking, so you can easily find it in your local hardware store.
Alaskan Yellow Cedar
There’s no doubt that Alaskan yellow cedar is one of the hardest types of cedar.
It gets its name from its distinctive yellow color, and fortunately, it is also available at long lengths.
White Cedar
Northern and southern white cedar are harvested from the south and southeastern parts of Canada.
Both the northern and southern varieties are very aromatic and are relatively rot-resistant.
They’re also close-grained and relatively easy to work, which makes them convenient for beginners.
Port Orford Cedar
Port Orford cedar is one of the more popular materials for planking, but it’s also used for interior finishes.
It’s easy to work, and you can find it in longer lengths than the other types of cedar on this list.
If you’re in the market for a wood type that will take quite a beating from tools , ash is one of the best to choose.
This material works well with sanding and sharp tools. Not to mention, it bends easily when exposed to steam.
Unfortunately, it’s not rot-resistant, so it’s not your best option for planking. Instead, it is great for frames, handles, poles, boat hooks, and more.
You can typically get your hands on cypress for the lowest cost if you live near the Gulf coast of the United States.
Cypress is a phenomenal wood for planking because its natural resin is fully resistant to dry rot.
Because these trees grow in the swamps along the Gulf, you can guarantee optimal water resilience.
Cypress is relatively lightweight with moderate strength, but it does tend to absorb a lot of water.
When your boat is submerged, it will be much more massive, so you won’t want to consider it for land transport.
For example, if you’re building a portage craft, cypress is one of the top materials to avoid using.
When deciding on elm for your boat, you will undoubtedly want to focus primarily on rock elm.
It’s one of the most prestigious woods due to its heaviness, strength, and resilience, which also makes it difficult to source.
Even if you live in the Northcentral United States, where it’s familiar, rock elm is challenging to get your hands on.
Still, no one can deny that rock elm is a phenomenal choice for boats because it offers optimal shock resistance, making it ideal for all water conditions.
You’ll also find that it creates an incredibly sturdy frame for the bottom of boats, while in England, they use it for planking.
If you can find rock elm for a reasonable price, it is surely one of the better types of wood to consider buying.

Out of all the other types of wood on this list, oak is the most prevalent in shipbuilding.
Because it is quite affordable and easy to source, it has become the go-to material for beginners and veterans.
Similar to cedar, there are a couple of different types of oak to consider.
Compared to red, white oak is far more popular because it’s relatively easy to work with and offers plenty of strength.
Many shipbuilders use it for longitudinal timbering because it doesn’t shrink or swell when it gets wet.
Also, it’s known to hold fastenings particularly well, so you won’t have to worry about taking extra steps for durability.
Regardless of how you purchase white oak, it is highly resistant to dry rot, making it easy to store.
There are a few similar traits between white and red oak, primarily its ability to bend with steam.
However, it’s the less popular of the two because it’s much softer and is more likely to absorb water.
You’ll have to make sure you pay special attention to painting and finishing the wood to protect it from water.
If you’re searching for a type of wood with strong roots in history, teak is your best option . It’s typically used for boat building in the East Indies and Burma.
The natural resin in its fibers is what makes it resistant to water soakage and dry rot.
The unique aspect of teak is that it can sit unfinished for years and never fall victim to elemental damage.
Most of the boats built with teak can last centuries, especially with expert craftsmanship. However, this also means that it’s one of the most expensive materials to get your hands on.
You’ll frequently find that teak is used on luxury cruisers, especially multi-million dollar yachts.
In North America, it’s unlikely you’ll be able to source enough teak to build an entire boat. Although, you can find smaller pieces for elegant finishes, such as rail caps and trims.
It’s not beginner-friendly due to its cost, and there is a minimal margin for error when working with such an expensive material.
Best Wood for Boats: Mahogany
One thing that most boat builders can agree on is that mahogany is the most available timber to have on-hand.
It is the type of wood that can have anything thrown at it, and it will handle it with ease.
Many things make mahogany your best option, apart from oak.
Mahogany has gained a reputation for being high-quality in several ways, especially as it’s made from heartwood.
With a natural resistance to rot and decay, as well as a phenomenal denseness, it’s ideal for preventing shrinkage.
It is frequently used with boating, but it is also a widespread material source for house building because of its resilience.
You’ll finally be able to use a timber that maintains your boat’s structure but also looks great over time.
Even though your boat’s framework is the most important, you’ll also want it to look professionally finished.
Mahogany has a classic and timeless appeal that is sure to suit the needs of any boater. It feels and looks luxurious, whether used for framing or finishing.
Another advantage of mahogany is that it’s easy to finish with varnishes, stains, and paints. You can easily customize the look of the wood to meet your every dream.
It’s easy for certain types of wood to look great and have elemental resistance, but are they easy to work?
Mahogany packs a powerful punch in machinery and hand tools, allowing you to work it with ease.
Even beginners won’t find it too difficult to use, so it can easily be specified to meet your requirements.
To get the most benefits from this wood, you’ll want to make sure you source it from a reputable retailer.
Ideally, choose someone who sources their wood sustainably to ensure quality and environmental protection.

It’s easy enough to listen to the advice of others when you’re looking for timber. However, you must remember you’ll need to find the perfect choice for you.
MyBoatPlans can help you to source the perfect type of wood for every part of your boat.
By taking the guesswork out of planning, you can use this comprehensive guide to make the most of your time.
You will learn about the dozens of wood species and why they’re recommended for specific applications.
You can also use the more than 518 step-by-step plans to decide which type of wood you’ll use for specific areas.
MyBoatPlans is not only an excellent resource for boat building but also all of your finishing touches.
With the help of the crystal-clear photos to guide you through the building steps, you can get inspiration for finishing touches.
All boating enthusiasts will find it much easier to create a custom aesthetic that is sure to turn heads with the help of MyBoatPlans.
When searching for the best wood for boats, it’s important to remember there’s plenty to choose from.
Some varieties might be better for the environment, while others could be more affordable due to their availability.
With expertly written guides, such as those from MyBoatPlans, you can easily find the perfect timber for every part of your boat.
4 thoughts on “Best Wood for Boats: Finding What Works for You”
Hi there just wanted to give you a quick heads up. The text in your article seem to be running off the screen in Ie. I’m not sure if this is a format issue or something to do with internet browser compatibility but I thought I’d post to let you know. The design and style look great though! Hope you get the issue solved soon. Kudos
Hello and welcome! Thank you for letting us know. We’re looking into it 🙂
This is the perfect web site for anyone who really wants to find out about this topic. You realize so much its almost hard to argue with you (not that I actually will need to…HaHa). You definitely put a fresh spin on a subject that has been discussed for ages. Excellent stuff, just wonderful!
Thank you so much for your kind words. We really appreciate it when you guys leave us comments…motivates us in sharing more high quality content 🙂
Leave a Comment Cancel Reply
Your email address will not be published. Required fields are marked *
Save my name, email, and website in this browser for the next time I comment.
Get your Boat Building Free Guide

Traditional Wooden Boat Building (Plus Video)

The two craftsmen inspecting a boat under construction, showcasing the art of traditional wooden boat building.
This time-honored practice merges precision woodworking skills with a deep understanding of marine architecture.
Construction in Progress:
The wooden frame laid out before us is the skeleton of the boat, known as the ribbing, which provides the structural integrity of the vessel.
Each rib or frame is carefully shaped and assembled to follow the contours of the boat’s design, ensuring stability and hydrodynamic efficiency.
Materials and Techniques:
Selecting the right wood is crucial in boat building; it must be durable, resistant to decay, and have the ability to withstand constant moisture.
The ribs are typically made of a hardwood, while the planking might involve a combination of both hard and softwoods.
Traditional methods such as steam-bending are often employed to curve the wood into the necessary shapes.
Precision and Skill:
The craft of boat building demands a high degree of accuracy.
The ribs must be placed at exact intervals, and the planking has to be watertight.
It’s clear from the image that these woodworkers have utilized their extensive knowledge to ensure that each piece fits seamlessly together, showcasing expert joinery techniques.
For Woodworkers:
Boat building is a challenging endeavor that requires an array of woodworking techniques.
Woodworkers must be skilled in shaping, joining, and finishing, often under the unique constraints that working with curved surfaces and structures presents.
Conclusion:
This boat, still in its formative stage, symbolizes the intersection of function and craftsmanship.
The construction process is a testament to the woodworkers’ skill and dedication to preserving the traditional methods of boat building.
For those in the woodworking community, the creation of such a structure is not just a testament to their craft but also an homage to the rich maritime heritage.
Not the same boat or project, but I found this video fascinating!
WHY DO SPIRIT YACHTS BUILD WITH WOOD
Wooden sailing yachts.
With so many composite products on the market today, the Spirit team is frequently asked about the intricacies of building modern yachts with such a traditional material. In summary, wood is the only natural boat building material offering beauty, impressive strength to weight ratio, flexibility and durability.
However, we’re aware that here at Spirit we’re pretty biased, so here are the facts….
Wood offers incredible strength without the weight of most fibreglass products
If used in combination with epoxy resin saturation (as we do at Spirit), and when considering the overall yacht structure, wood is a far superior material to the modern composites used across our industry today. With its fibrous grain imbedded in a naturally intricate matrix, wood offers impressive strength without the accompanying weight of most fibreglass products.
When comparing the strength to weight ratio of a wooden yacht to a fibreglass composite boat it is necessary to consider the two construction processes. When building a fibreglass composite structure the hull is either made up of multiple layer of heavy E-glass, or a core is added such as foam or balsa. These cores increase the complexity and cost of the structure, and also require additional reinforcement in the form of pad layers where bulkheads and loaded structures touch the hull. As E-glass is heavy (but low cost) the result is an equally strong structure but with a weight penalty and none of us want to sail with excessive weight on board. With wood, the skin thickness comes as part of the material, with the added advantage that timber can sustain impacts with far less damage to the structure due to the wood’s complex multi-directional grain. At Spirit we also don’t have to use composite moulds as all our yachts are handcrafted using wooden ring frames, thus allowing us to tailor the design to the owner’s requirements.
Wood offers impressive flexibility and durability
The natural matrix of wood offers exceptional flexibility, allowing it to easily be shaped, formed and bonded. This allows us to create intricate shapes without the need for heavy reinforcement.
Spirit hulls and decks are internally finished by hand, unlike most composite yachts where a lining is required to complete the inside of the hull. Not only aesthetically beautiful, the natural wooden finish of the interior of a Spirit yacht provides excellent insulation, both thermal and sound, due to the impressive vibration absorption characteristics of wood. The added thermal insulation also means our yachts don’t suffer from the condensation that affects many fibreglass composite boats.
Spirit’s high quality timber and sustainability credentials
Wood is at the heart of everything we do at Spirit and Sean (McMillan) has always been meticulous in sourcing the highest quality timber without compromising on sustainability . We are committed to only dealing with responsibly managed forests and regulated suppliers.
Boundless beauty
We may be biased but with their iconic clean lines and warm wood finishes there is no denying the outstanding beauty of Spirit’s modern classic yachts . The ultimate combination of the stunning wooden aesthetics with modern appendages and the latest in sail technology means Spirit yachts have beauty, style and performance; what’s not to love?
RELATED ARTICLES
Spirit p35 e.f.
STAY IN THE LOOP
" * " indicates required fields
Yachting Monthly
- Digital edition

Boat building: what will yachts be made from in the future?
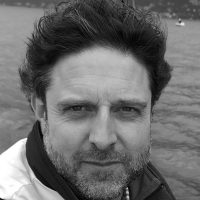
- Sam Fortescue
- December 17, 2021
Sam Fortescue shines a light on boat building jargon and looks into a future devoid of fibreglass
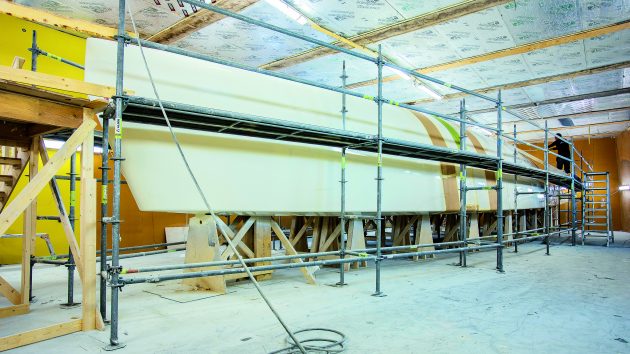
Building with pre-preg materials is efficient, but the hull must be 'cooked' at a precise temperature to cure it. Credit: Eva-Stina Kjellman
The end of GRP? Sam Fortescue looks at past, present and future boat building materials
Glance at a brochure for a new boat or walk the pontoons at the Southampton show and you may have come across some terms that didn’t mean much to you.
The art of boat building is as recognisable as ever, but the science of it is constantly developing. New materials and new techniques can make it hard to compare like with like.
Take wood, for instance: the material of boatbuilding choice for millennia.
There are still plenty of wooden boat-builders out there, labouring away in dingy sheds and halls to craft pilot cutters, rowing skiffs and other emblematic vessels of yesteryear.
But perhaps the best known of the wooden boatbuilders is Spirit Yachts in Ipswich, building thoroughly modern boats – in composite wood.
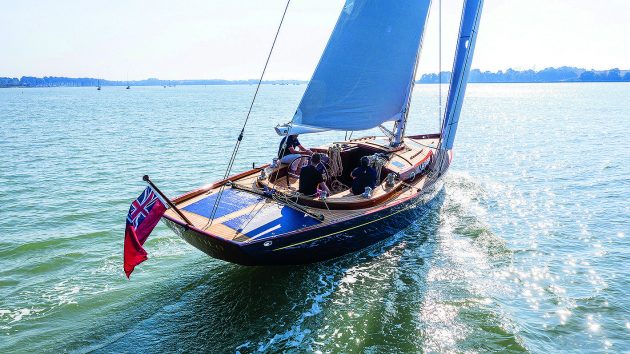
The Spirit 44E is a ‘zero carbon’ cruising yacht. Credit: Richard Langdon
‘Certainly we use epoxy resin to bond the components together, but the amount of resin used is minute compared to GRP or carbon,’ says founder and head designer Sean McMillan.
‘Both carbon-fibre and GRP rely totally on being saturated with a high density of polyester or epoxy resins to impart structural integrity. Wood, whilst also a linear fibre material, is cross-linked with a cellular structure entirely created by nature and has full structural integrity in its own right.’
In fact, the 1.6-tonne Spirit 30 daysailer employs just 73kg of resin and 12.2kg of hardener in its entire construction.
‘In 20 years’ time, when GRP has become socially unacceptable – not to mention any future end-of-life legislation – who knows, we may look back and see the last 60 years of GRP boats as a historical niche,’ finishes McMillan defiantly.
Another example is racy French builder RM Yachts, whose boats are famously swift, with offshore hulls designed by Marc Lombard.
And yet they are built in plywood and epoxy.
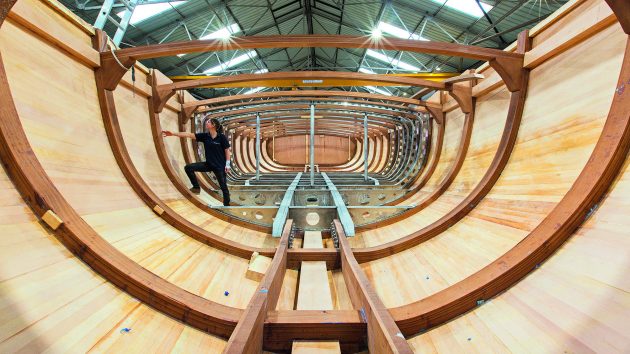
Thought every Spirit yacht us built of wood, it is a composite of glue and epoxy sheathing.
It is flexible, robust and far more sustainable than standard glass-reinforced plastic.
Sheets of laser cut Okoumé plywood up to 22mm thick are bent around a mould and epoxied to plywood structural members.
The whole lot is also epoxy sheathed for longevity.
It’s a technique which means that the brand-new RM 1380 is 9.8 tonnes light – slightly less than the comparable X4-6 from X-Yachts.
‘Plywood is the soul of an RM. It a very useful material, allying a good stiffness with lightness – perfect for building the hull and the structure,’ says head of engineering Edouard Delamare.
‘But plywood is nothing without epoxy, because it ensures the waterproofing – vital in a marine environment.’

Boat building using glass-reinforced plastic
Many series production yards, from Beneteau to Bavaria , still use the most basic form of wet lay-up – splurging resin on to mats of glassfibre with a roller to get them well wetted out before laying down the next layer of glass.
It is very hard to control how much resin is applied and there are often air pockets between layers.
For this reason, hulls built this way tend to be overbuilt and heavier.
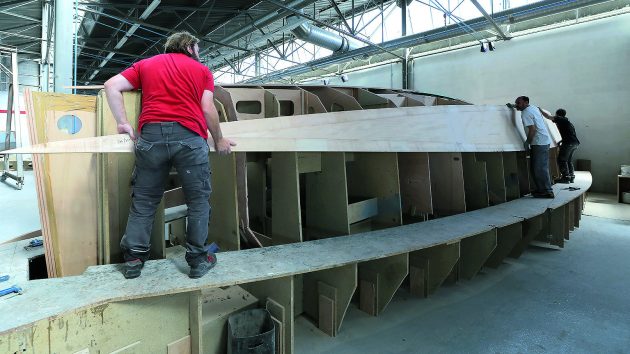
RM Yachts is unique in building its offshore yachts in plywood and epoxy
Polyester is the cheapest and most commonly used resin, but it can bond with water, creating the problem of osmosis.
That’s why isopthalic gelcoats are applied to the outside of the hull, to act as an effective barrier to moisture.
Vinylester creates many more bonds than polyester and is reckoned to be up to three times stronger, but it costs more too.
And epoxy is the best performing resin of all, used only in high-quality lay-ups. All are pretty toxic, and sport the ‘dead-fish’ icon on the side of the tin.
When vacuum infusion emerged as an industrial technique in 1990, it allowed boatbuilders to use less resin and spread it more evenly around the finished panel for greater strength.
But it generates a lot of waste, because each infused part has to be prepared with a host of plastic layers.
Besides the plastic of the vacuum bag itself, there’s a breather layer to distribute the resin and a peel ply to stop it sticking to the infused part; a thick bead of sealant tape; disposable feeder tubes are required every few inches, and many of the vacuum tubes must also be binned.
The technology has not stood still, though, and there are now reusable vacuum bags made from inert silicon, for instance.
Some bags have the mesh structure necessary to spread the resin built in, while the aerospace sector has pioneered the use of PTFE membrane that stops resin clogging up the vacuum pump side of the system.
Sweden’s Arcona builds its fast cruisers using vacuum infusion, and has for many years.
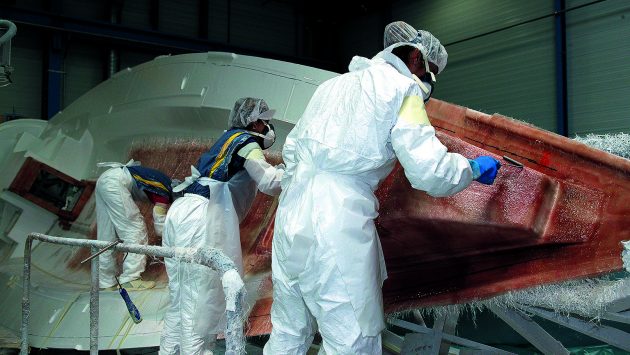
Hand lay-up is a process that has changed little over the years of boat building
But in order to add strength and stiffness, it laminates in a steel support frame amidships to transfer the loads from the rig into the keel.
Improvements in lamination techniques mean that the boats are lighter than ever.
Late Arcona designer Stefan Qviberg said the current Arcona 40 displaced a whole tonne less than its equivalent a decade earlier.
Other boat builders use other types of reinforcing for the high-load areas of the hull.
Aramids like Twaron and Kevlar often feature, as do selective areas of carbon-fibre on stringers and around keel bolts and chainplates.
High-end yacht builder Baltic uses carbon reinforcing, for instance, to add strength without extra weight.
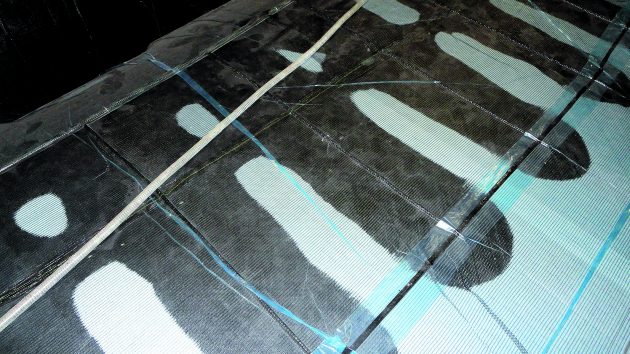
Vacuum infusion uses less resin but creates a lot of plastic waste
Performance catamaran brand Catana likewise uses Twaron and carbon in its lay-up to save hundreds of kilos; some 700kg in the old Catana 47.
Some claim that aramid reinforcing makes a hull safer, for example in the event of collision with a container, but others refute this.
Naturally enough, carbon is still the ultimate performance material because of its blend of strength, stiffness and light weight.
It is also prohibitively expensive relative to other fibres and very resource-intensive to produce, as it requires temperatures up to 3,000º C and a plastic feedstock.
The bulk and waste of the infusion process has led to another step forward in the form of so-called pre-preg materials, where the sheets of fibre used to strengthen the hull come ready-coated with a pre-catalysed form of the resin that reacts very slowly at room temperature.
Instead of needing to mix epoxy with hardener and reduce its viscosity with toxic styrene to draw into the mould, a precisely-controlled curing process activates and sets the resin.
The result is a stronger, lighter laminate than can be produced through wet lay-up.
Gurit’s SPRINT system goes a step further by sandwiching a thin film of heat-activated resin between two layers of fibre.
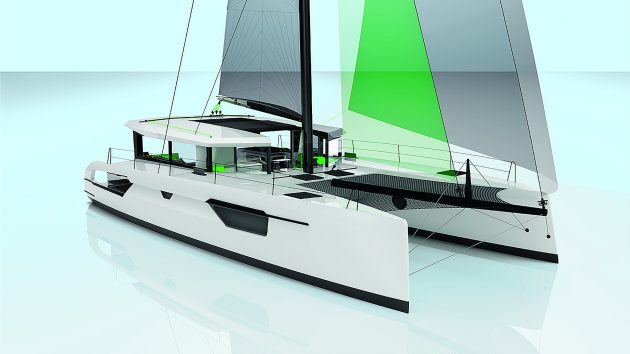
Windelo uses basalt fibre to strengthen its hulls during the boat building process. It is said to be much less carbon intensive than using glass
The advantage of this is that the fibres remain dry until curing so air can be more easily removed under vacuum to produce a laminate with a void content of less than 0.5%.
Baltic Yachts uses this technique, building an oven around its hulls to cure them.
‘With one or two exceptions, we haven’t infused a boat for some time,’ says CEO Henry Hawkins.
‘Using Sprint and pre-preg materials saves weight compared to vacuum infusion. With hand lay-up, generally more resin is mixed than needed and a lot gets discarded. This is the same with infusion where resin is lost or wasted in the plastic hoses and pipes and breather film and within the distribution channels.’
Continues below…
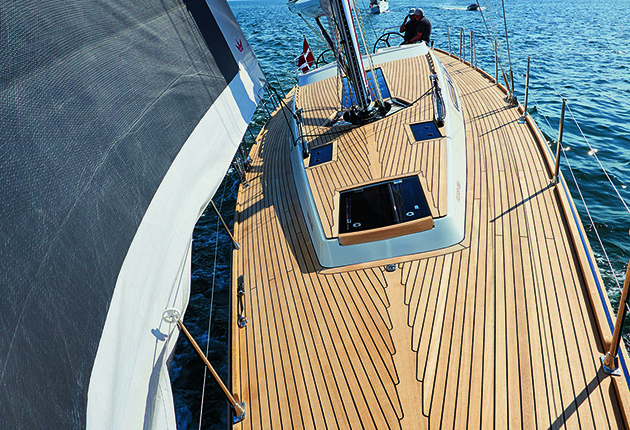
The dirty truth about teak
Teak is beloved by boat owners and shipyards for decking and yacht building, but any claims that it is sustainably…
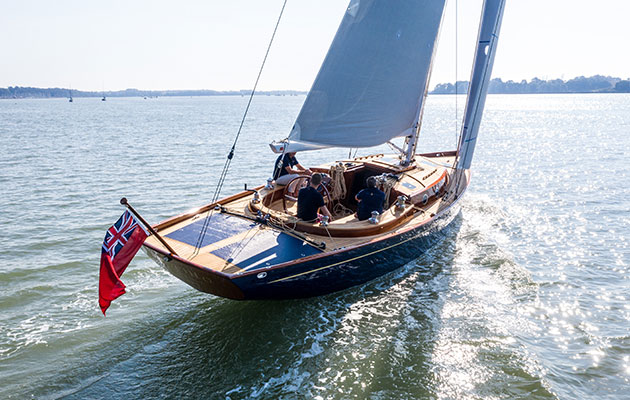
ON TEST: Spirit 44e – the sustainable future of sailing?
A wooden boat that blazes a trail for modern technology and sustainability sounds too good to be true. Theo Stocker…
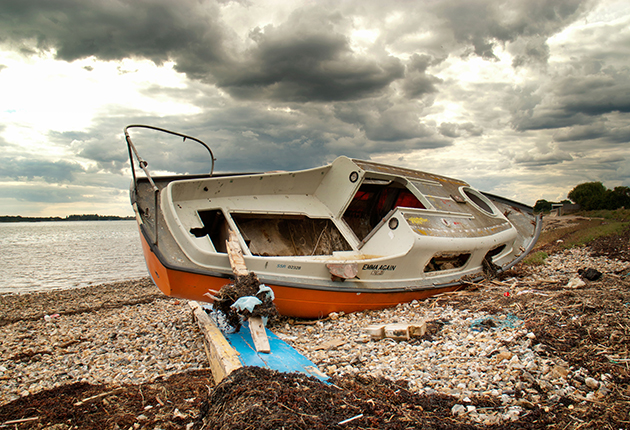
What’s the future for derelict GRP boats?
With 9,000 GRP boats abandoned in Europe each year, finding disposal solutions isn't easy. Could new technologies be the answer?…
Even at this sharp end of the composite business, rapid advances are being made – driven by aerospace and Formula One.
‘We can now take away the expensive autoclaves and ovens – they can cure at ambient or 40-60ºC,’ says Ashley Parkinson, a research engineer with the UK National Composites Centre.
‘It’s a more expensive process to use, but in the high-performance market, it’s worth it.’
Greener composites
Now, there is nothing particularly sustainable about producing glassfibre – a technique that involves heating raw silica to 1,370º C, then pultruding the molten strands onto a bobbin.
You can use some recycled glass to lower your emissions, but it is an energy intensive process and it is very hard to extract the raw materials from end-of-life fibreglass.
Swiss supplier Bcomp tested alternative natural fibres 10 years ago, when it was a start-up in a garage.
‘Flax turned out to be the best in terms of mechanical properties, soil usage, water requirements and overall performance,’ explains marine and industry manager Paolo Dassi.
It actually locks up carbon rather than producing it – as much as 500g of CO2 per kilogram of flax.
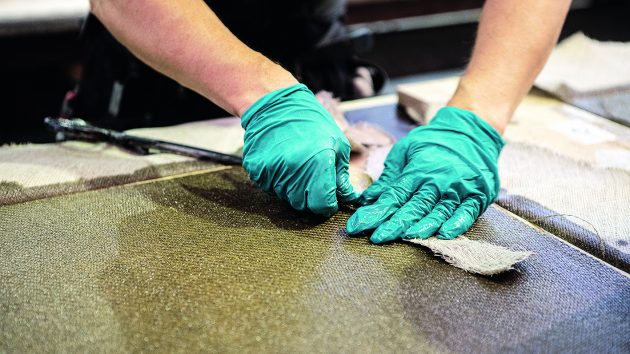
Precise cutting is key to reducing fibre wastage in boat building
‘The plant acts as a CO2 sink during its growth. This completely offsets the CO2 emissions of the manufacturing stages.’
Bcomp’s extraordinary growth began when it managed to process the flax stems to be of uniform size and flatness, replicating the grades possible using glassfibre.
Its AmpliTex product is available as a unidirectional, stitched biaxial or woven twill, ranging from 200-500gsm.
In lamination it is 50% stiffer than glass and just a little weaker, making it an ideal substitute.
Couple this with an extra flax mesh called PowerRibs, and you end up with a composite that closely resembles carbon, but with just 25% of the emissions.
AmpliTex has already been used in niche boat building projects, including the glorious Flax 27 daysailer by Green Boats of Bremen, which sports cork decking.
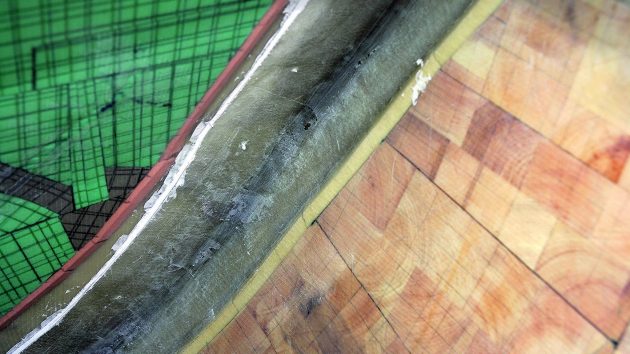
Foam sandwich hull construction (green) or balsa core (wood) is much stronger, for little extra weight. Credit: Graham Snook/Yachting Monthly
It was a key part of the lay-up of the new Café Racer 68 from Baltic. Although her hull is in carbon, 50% of the structural members were in flax composite.
France’s Windelo has taken a different tack in its catamarans.
It uses basalt fibre – made from melted volcanic rock – which ‘is slightly stronger than E-glass and just one-10th as carbon intensive to produce and use’.
Its first 50-footer has a hull that also features a recycled PET foam core for strength and stiffness. But it is not just the fibre that is being decarbonised.
So-called ‘green epoxies’ have been developed, where a significant chunk of the synthetic oil-derived molecules of the resin are replaced by bio-sourced molecules.
Gurit’s Ampro for hand laminating is 40% bio derived, for instance.
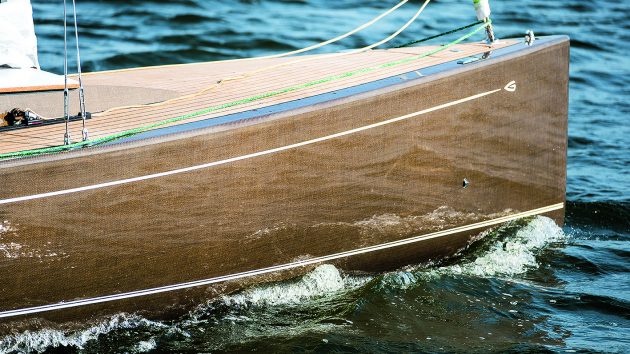
Green Yachts focuses on environmentally-friendly boat building techniques. Its Flax 27 is built of sustainable flax fibre
And the ProSet range from West Systems includes epoxies containing up to 30% bio molecules.
They can essentially just be dropped into any process that would have been suitable for the equivalent synthetic resin.
‘Any customer that is familiar with epoxy processing, vacuum consolidation or post curing will be very familiar with the process,’ says David Johnson of Wessex Resins, European manufacturer for West.
‘Even wet lay-up with no vacuum bagging.’
There is a modest cost increase, but it amounts to less than 25% compared to a standard epoxy, and a drop in the ocean of the boat’s overall build.
‘Bio-based epoxies are more expensive because there’s more sophisticated chemistry involved,’ says Johnson.
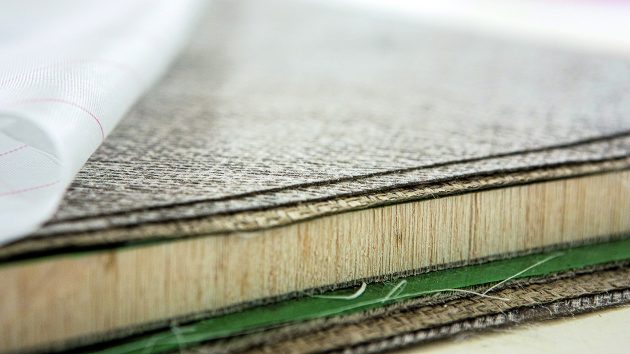
Pre-preg flax fibres being laid up around a balsa core
‘Compared to building a boat in vinylester or polyester, you can use slightly less material because of the superior qualities of epoxy. The end cost differences are negligible and there are benefits in lighter weight: you become more efficient, and the loads are less.’
Suppliers like Gurit are also finding ways to substitute the synthetic foam core used in sandwich hull construction.
Standard foam is made of virgin PVC, with all the associated environmental pitfalls.
Gurit has developed more renewable alternatives using up to 100% recycled PVC and balsa wood.
Builders from Arcona and X-Yachts to Bali and Gunboat catamarans use foam cores in their lay-up to build boats that are stiffer and lighter than they would be otherwise.
Away from composites
Some innovative new boat builders are going in another direction altogether, eschewing the by-now traditional GRP for something that can be genuinely reused repeatedly.
Start-up Vaan is building its 42ft R4 catamaran out of a grade of aluminium alloy commonly used in window frames and road signs, so up to 60% of the hull is already recycled.
‘There’s no way to distinguish it from virgin material,’ says Vaan founder Igor Kluin.
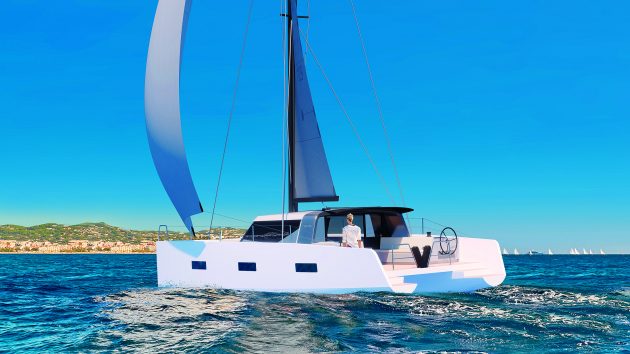
Vaan uses a high proportion of recycled aluminium to build its hulls, which can then be easily recycled
It hasn’t been easy to secure supplies, however. That’s partly because window frames last for 50 years or more and also competition with other sectors.
‘In the short term the costs are higher because there are so many people jumping on the bandwagon, but it has only 5% of the energy use of virgin alloy, so in the end it should be cheaper.’
Vaan’s novel approach to sourcing more sustainable materials extends to the interior finish as well.
It uses a pineapple leaf fabric instead of leather, plentiful European poplar for cabinetry, cork instead of teak decking and recycled PET.
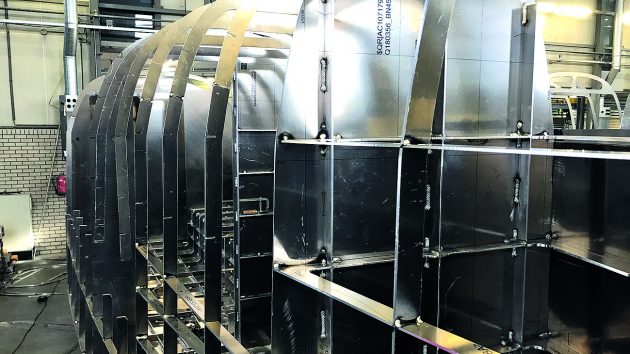
Greener boat building: A hull made from recycled aluminium
Parts of the boat are 3D printed – something that higher end brands are doing more and more of.
‘Recycled industrial PET is being 3D printed for the back of the Vaan spoiler because it produces a lower volume than moulding,’ says Kluin.
‘We want to see if it can become load bearing. We’re also 3D printing with aluminium, too. It’s useful for smaller structural elements that are hard to reach and would traditionally have been milled.’
Recyclability of boat building materials
Besides wood, all forms of composite suffer from the same problem; at end of life, it is very difficult to separate the component materials for re-use.
This is why using materials such as steel or aluminium can make sense, despite the higher environmental cost of the virgin metal. They can be reused repeatedly.
The composite recycling systems developed to date, which include pyrolysis, burning and shredding, are all unsatisfactory because of the energy intensity of the processes or the fact they yield a lower quality material that has to be downcycled.
In principle, it is possible to use resins that melt again at high temperatures and can be collected, refined and reused.
Elium resin from Arkema is capable of exactly that, and is already being used in recyclable wind turbine blades.
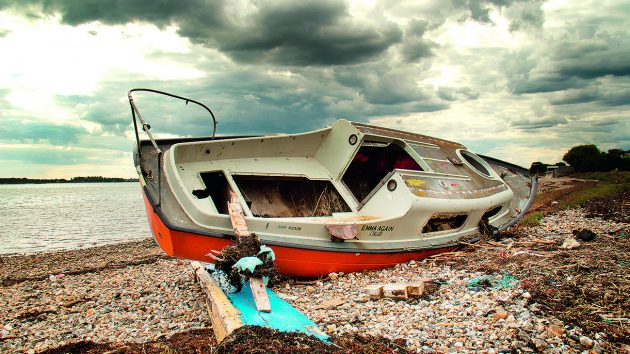
Laminate are expensive to separate for re-use. Credit: Rob Wilkinson/Alamy Stock Photo
They even built a 6.50m Mini Transat boat from it.
The process also yields reusable glass, but carbon and flax don’t support the heat: carbon loses as much as two-thirds of its strength and flax simply combusts.
However, an Australian study has shown how carbon-fibre composite can first be heated without oxygen in a pyrolysis chamber to burn off resin, then oxidised to yield carbon-fibre with most of the strength of virgin fibre but only 10% of the environmental impact.
Cured laminates can also be separated using a chemical process proven in the lab at the National Composites Centre, with a big vat of acetic acid.
Portsmouth University is researching enzymes to decompose plastic, starting with plastic bags.
The approach could eventually handle boats as well.
‘You have to find the right enzyme that works for snipping the molecules of a particular polymer. Practically, it’s a decade away,’ says Ashley Parkinson of the NCC.
- Canoe Building
- Bay Hawk Canoe Building
- Rob Roy Canoe Building
- Whitehalls and Wherries
- Kayak Building
- Boat building Kits
- Boat Building DVDs
- Incidentals
- Planking Bits
- Fiberglass Cloth

- Journals & Articles
Wood Types and Uses
Posted in Articles .
WHICH WOOD IS RIGHT FOR YOU?
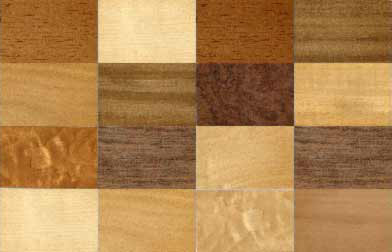
White ash is similar to oak in strength, hardness and shock resistance. It is failrly easy to work wth sharp tools, sands well and bends well under steam. Though it is rot resistant, It is not suitable for planking. It is primarily used in smaller round bottom hulls for frames, oars, boat hook, breasthooks, handles and poles. The weight per foot cubed is 42 lbs.
There are a number of different kinds of cedars native to different areas primarily in the US. These woods are more or less similar in mechanical characteristics. They are light weight and easily worked, however they are somehat subject o fracturing. Most are available in long lengths with straight grain free from knots. These woods should be predrilled prior to using screws or nail to avoid splitting.
Alaskan Yellow cedar - is one of the strongest and hardest of the cedars. Due to its coloring it is also known as yellow cedar and is available in long lengths and weighs in at 32 lbs per cubic foot. Port Oford Cedar - is light brown in color with little variations with a course texture. It is easily worded and comes in very long lengths. It is light weight and favored as planking material, but is also used widely for interor finishing. it weighs in at 29 lbs/ foot cubed.
Western Red Cedar - is the softest of the cedars, has the least tensile strength and as a results, bends very well. Not typically used for planking except for small strip built craft because of its tensile strength, however when encapsulated in epoxy and fiberglass makes a fine small craft. Readily available because of its widespread use in outdoor furniture and decking. it weights in at 30 lbs / foot cubed.
White Cedar - There are two varieties of white cedar. The Northern type is native to the Great Lakes region and southern Canada, The Southern type grows in the coastal regions of the southeastern seaboard. Both varieties are very similar in that they are fine, close-grained woods with an aromatic odor are easily worked and are fairly resistant to dry rot. It is the favored planking for small boats and skiffs.
Unlike the Western cedars. it is rarely obtainable free of knots. These are usually small. and if light do not adversely affect tensile strength. Cedar swells easily and quickly when wet, which is one of its advantages as planking. It is also popular for fine interior joinery work. Average weight per cubic foot is about 23 pounds.
This timber is sometimes called b lack cherry due to its color. and was much favored in the earlier days of boatbuilding. It is less commonly available today and is expensive. It takes finish well, has a close grain and , a dark red color. If well seasoned, it rarely warps or checks. It was formerly much used as naturally grown crooks for breasthooks and hanging knees. It is too stiff and hard for steam bending. Weight per cubic foot is about 34 pounds.
This timber is common in the southern United States and along the Gulf coast. It is highly favored for planking as it has a natural resin which resists dry rot. It is fairly light and moderately Strong. and available in wide and long timbers. Its one disadvantage is that it soaks up an inordinately large amount of water when immersed and becomes heavy. It is therefore used mostly in heavy or commercial craft where land transport is not contemplated. Weight per cubic foot is 32 pounds.
This is rock elm and not American or slippery elm which is not suitable for marine use as it is a very soft wood low in tensile strength. Rod elm is a very strong, hard wood with great shock resistance and is readily bent into hard curvatures when steamed. It is popular for framing round bottom skiffs and canvas covered canoes. It is most popular in England for planking. Its native habitat is the Northern central regions of the United States, and it is unfortunately becoming quite scarce. Weight/ cubic foot is about 36 pounds.
Commonly known as Douglas fir. this is a strong. hard, and somewhat heavy wood with rather coarse grain. It absorbs water readily. as in the case of cypress, and takes up much weight ill the process. Its main disadvantage is its low resistance to dry rot. and it was formerly used mostly as interior framing, sheer shelves, bilge stringers. and derrick masts. In recent years it has come into widespread use as planking. particularly in commercial vessels when specially treated with wood preservatives. It is nowadays produced in tree farms by forest products concerns. and is readily available. Vast quantities of fir are made into various grades of plywood. Weight per cubic foot is about 28 pounds.
Also known as larch or tamarack. it is a very heavy and densely grained wood and is usually found as natural crooks and grown knees for framing purposes. It is becoming scarce and is usually found , if obtainable. from marine timber specialists. Average weigh t per cubic foot is 36 pounds.
Honey Locust
This is a very heavy hard wood with a close dense grain that resists splitting and abraiding and is very impervious to dry rot. It is the classic: material for mooring bitts, cleats, wedges, strongbacks, trunnels. tillers, and steering wheels. hatch coamings and any other area where a hardwearing wood , is required. It is difficult to work and requires very sharp tools to finish. Weight per cubic foot is 43 pounds.
Oaks ( red and white)
White oak is the timber of choice for ship and boatbuilding. It is principally used in framing and main longitudinal timbering for its density, hardness, great strength ability to hold fastenings and lack of shrinking and swelling when wet. When green, it is highly suitable for steam bending in smaller diameters. but this must be selected as such as it is not suitable for this use when dry or seasoned. In any case, it is very resistant to dry rot.
Red oak has similar qualities, but is somewhat softer and is more susceptible to water soakage, making it a second choice for marine use. Red oak must be paint finished if used for exposed areas above decks for hard wearing areas, as it turns black when exposed to air and will not take a varnish finish. Weight for both types is about 48 pounds per cubic foot.
Pine, White
There are several varieties of white pine used in boatbuilding. One is the Northern white pine which is native to the eastern United States. The other is the Western or Sugar pine of the west coast. There is another western variety called Ponderosa pine which is less favored. These woods share the common qualities of uniform texture, ease of working. light weight. good retention of paint. and fair resistance to dry rot. It is a favorite material for interior joinery and trim. It is sometimes used for planking but absorbs much water to gain weight as does cypress, The weight is about 26 pounds per cubic foot.
Pine, Southern or Yellow
Longleaf yellow pine is a favorite wood for planking as it is dense, hard, and strong and is readily obtainable at moderate cost in long, clear lengths. It is best when specially cut for marine work as quarter or edge sawn. It's one disadvantage is that it contains a heavy resin which will bleed through paint finish in hot weather. although this quality aids in making it resistant to dry rot . It is mostly used in commercial vessels. In yachts where a fine finish is desired, it has its place in interior framing, as it is very Strong and holds fastenings well. It weighs about 38 pounds per cubic foot.
Pine, Oregon
This term is sometimes applied to Douglas fir, which is not a pine, but it is mentioned to clarify its name.
This wood is noted for its resistance to dry rot, and is often used for interior joinery for its beautiful color when oiled or varnished, While sometimes used to plank small skills, its value is limited as its tensile strength is poor and it is easily shattered by impact. ][s weight is about 28 pounds per cubic fool.
Spruce, Sitka
This wood is light in weight and is moderately hard and tough with smooth fibers. It is very strong for its weight, and has long been used. for masts and spars. In the earlier days of aero plane manufacture, it was the material chosen for fuselage and wing spars. It is usually available in very long lengths. It is not highly rot resistant and must be kept sealed with paint, varnishes, or wood preservatives. It is now quite expensive. It weighs about 27 pounds per cubic foot.
Spruce, Eastern
This wood is native to the maritime provinces of Canada and the New England area of the United States. Its weight and general properties are similar to the Sitka variety, except that it shows many knots and clear stock is unobtainable. It is often used for planking and decking, although it must be carefully maintained to avoid dry rot.
This is a heavy dense hardwood and is mentioned because it was once favored for interior finishing of fine yachts. It does not markedly shrink or swell with moisture. Its weight is 39 pounds per cubic fool.
African Mahogany
This timber is obtained from the Gold Coast and Nigerian areas of Africa. The mature trees are almost uniformly of immense size and may be up to seven or eight feet in diameter. It is a rather soft, light wood with large pores but has a spectacular graining with many variations as to burling and pattern. It is largely used as facing on fir plywood panels. Its average weight is about 33 pounds per cubic foot.
Honduras Mahogany
This term is used to describe most of the mahogany-like timber in southern Mexico and Central America. It is heavier and stronger than the African variety and has a more dense structure. It is usually straight grained, holds fastenings well, and takes a very handsome finish. It weighs about 36 pounds per cubic foot.
Peruvian Mahogany
This timber is native to the region of the upper Amazon, in parts of Ecuador, Peru, Bolivia, and Brazil. Its great expense is due to transporting it from its secluded location. It is somewhat heavier and darker than the Honduras type, is straight-grained and resists splitting. It is perhaps the finest of all the boatbuilding woods, and has been utilized mostly in the better-finished yachts, as it is very durable and takes a very fine finish. It weighs about 39 pounds per cubic foot.
Philippine Mahogany
This is not a true mahogany, but is listed here due to its popular name. It is in reality a mahogany-like native timber of the Philippine Islands, and includes several related species. It is lighter in weight than genuine mahogany, holds fastenings well, and resists splitting. It swells but little on immersion and is easily worked. Due to its porous grain it does not take varnish well, and is usually paint finished. Large quantities of this timber have been exported to the United States and other countries for use in stock boats built in series production. It weighs about 38 pounds per cubic foot.
A native tree of the East Indies and Burma, teak is the most noble of all boatbuilding woods. Due to a natural resin within its fibers. it resists dry rot and water soakage, and even when left unfinished it appears to last indefinitely. Boats built of this wood have been known to last for centuries. It is characteristically a very heavy and hard wood with dense fibers. It is naturally a light gray or tan which bleaches out to almost a white color on exposure to the sun and salt water. It has long been a favorite for finely finished yacht decking, if used in no other place. Due to its very high cost, it is generally used today as trim material for rail caps, hatches. coamings, pin rails, and other areas subject to hard wear. On the debit side, it is very difficult to work as the resin content quickly takes the edge off the sharpest tools. Due to its high cost, it is seldom employed uhless the builder has a high degree of skill in boat carpentry and joinery. It weighs about 48 lbs / foot cubed.

Sandy Point Boat Works PO Box 687 Carver MA 02330

CLICK HERE TO EMAIL US!

508-878-8057
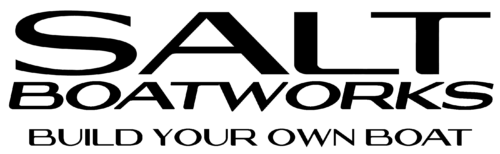
- $ 0.00 0 items
Build Your Own Boat!
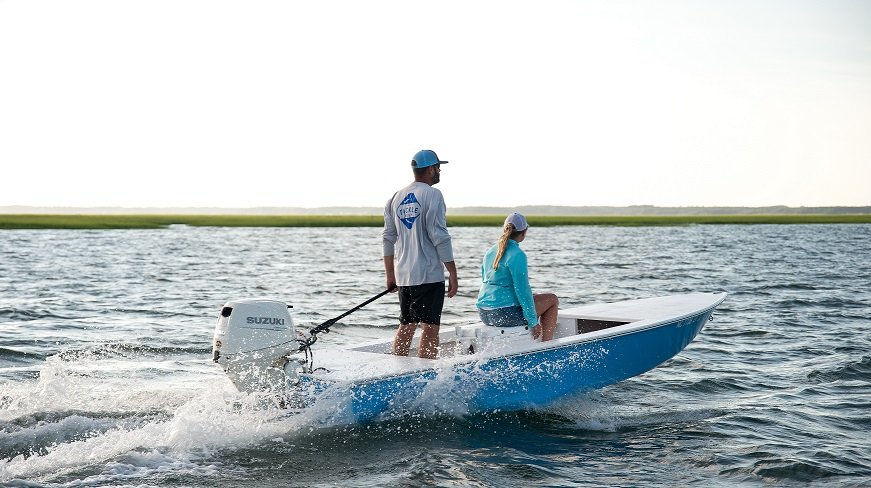
Stitch & Glue Designs
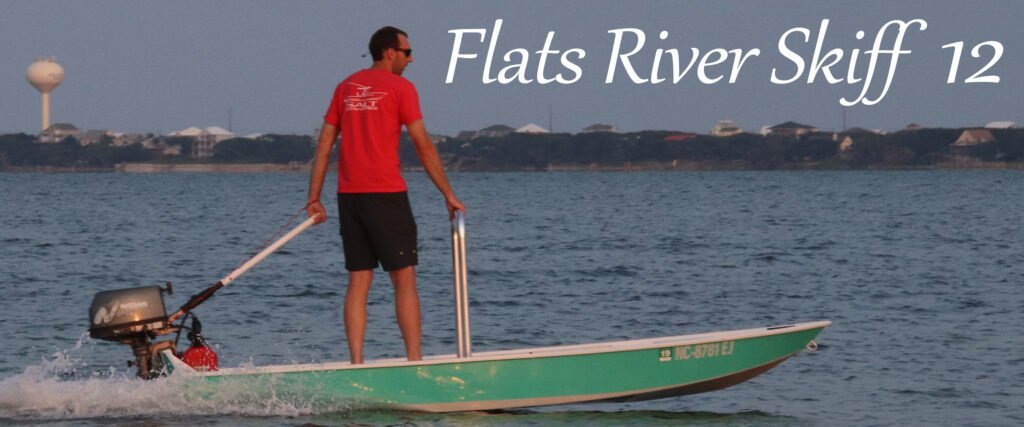
The Flats River Skiff 12 is a light, compact and stable solo skiff to access shallow water.
- 2″ – 4″ draft
- 1 person max
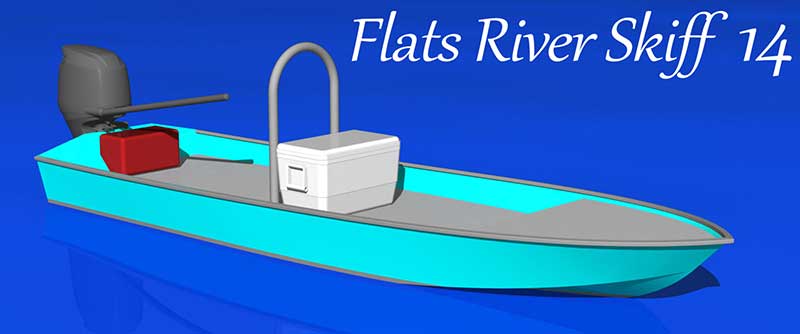
The Flats River Skiff 14 is the big sister to the FRS-12 , a light weight 2 person solo style skiff.
- 4′2″ beam
- 3″ – 6″ draft @ 825 lbs
- 2 people max
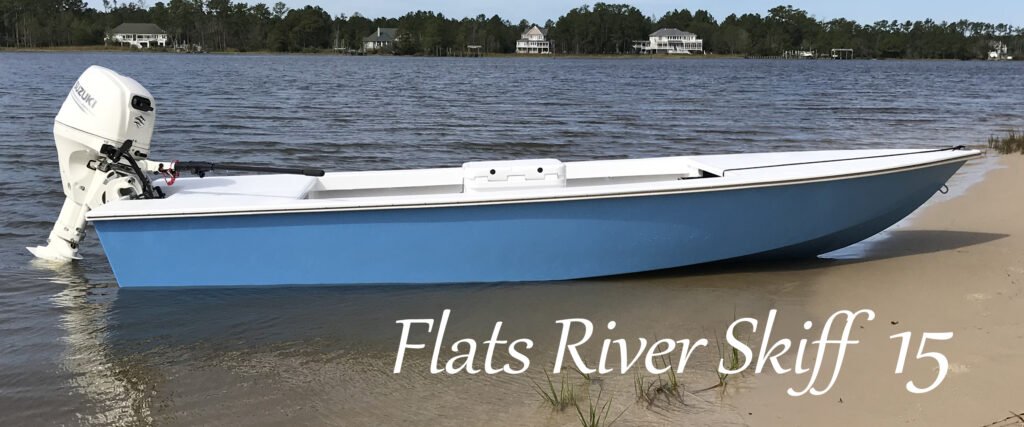
The Flats River Skiff 15 is a flats style 2 person shallow water hunting & fishing boat.
- 15′ LOA
- 5’4″ beam
- 5″ – 7″ draft
- 3 people max
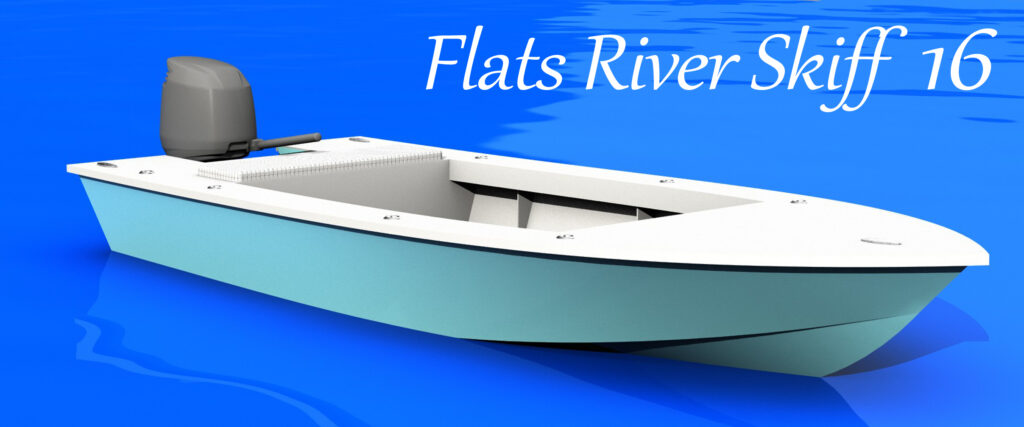
The Flats River Skiff 16 hits the sweet spot for a 3-4 person shallow water fishing boat.
- 16’7″ LOA
- 6’3″ beam
- 8″ – 10″ draft
- 4 people max
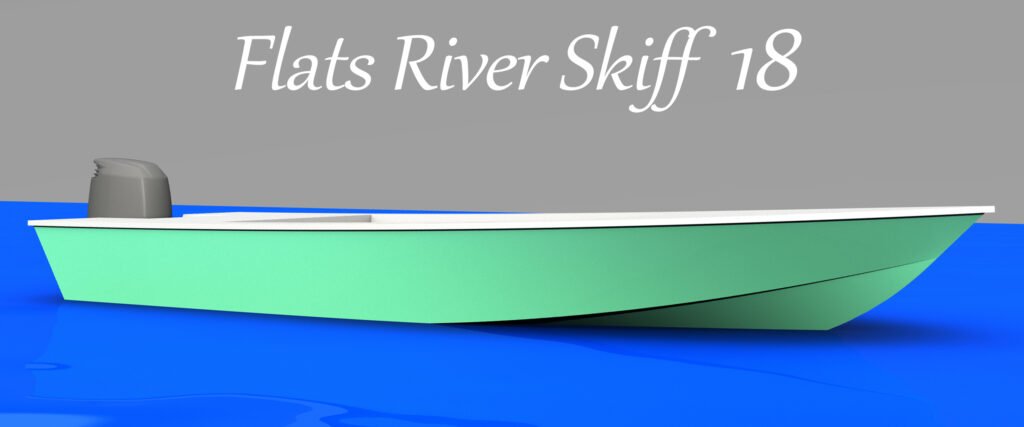
The Flats River Skiff 18 is the perfect bay and flats fishing boat.
- 18’6″ LOA
- 7’3″ beam
- 8″ – 11″ draft
- 5 people max
Cold Molded Designs
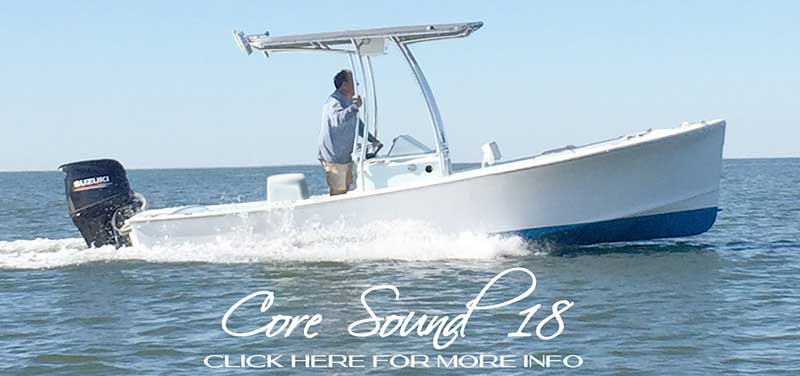
The CS-18 is a smaller version of our original CS-21 for those looking for a smaller boat with lower freeboard to inshore waters.
- Cruise 25-30mph
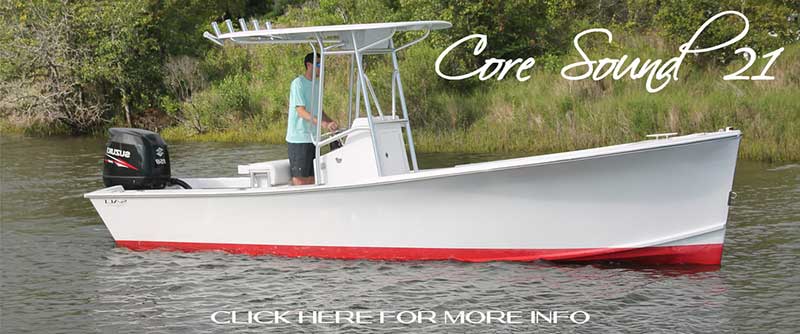
The CS-21 was inspired by the iconic Harkers Island style work boats. This center console design features unmistakable lines, a Carolina flared bow and a modified V bottom.
- 10″ – 12″ draft
- Cruise 30mph
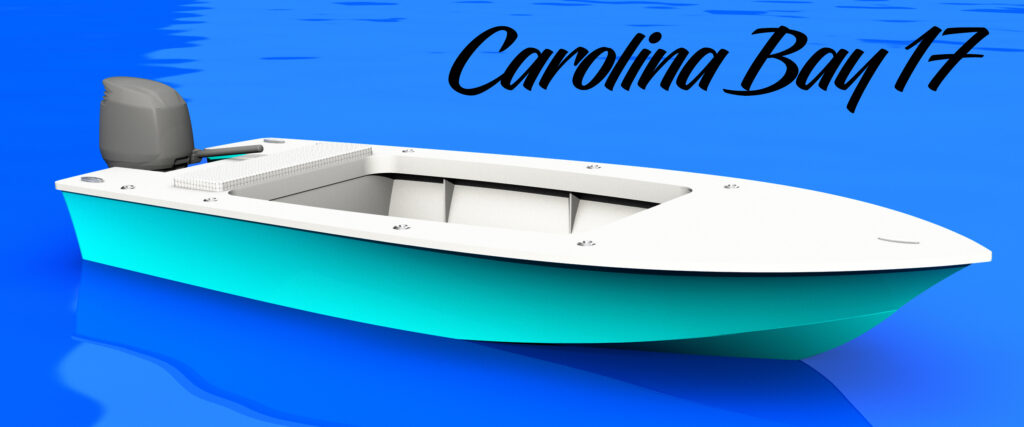
The CB-17 is the sister design to the FRS-16. She stands out as a custom flats boat with Carolina flare and rounded transom.
- 17′ LOA
- Cruise 25mph
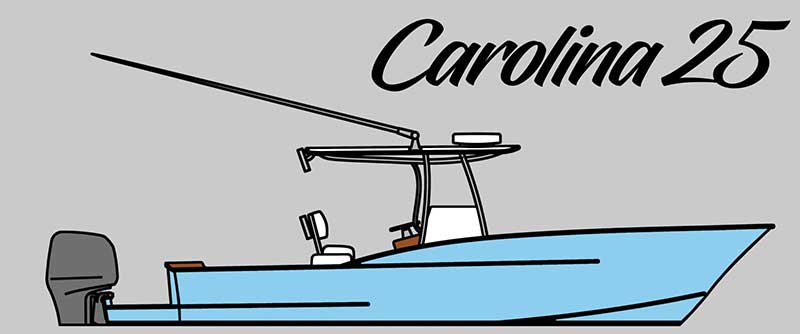
The C-25 is a North Carolina sport fishing boat in a trailerable center console layout. With Carolina flared bow, broken shear and tumblehome she is an iconic design.
- 28′ LOA (25’2″ hull)
- 8′6″ beam
- 16″ – 18″ draft
- 350hp single or twin 200hp max
- Cruise 30-35mph
More Info and Helpful Links
How to videos, plans & kits.
Located on Galveston Bay, Craven Boatbuilding is a full-service marine woodworking facility serving the Houston and Galveston yacht community, the Southern antique mahogany runabout market and the custom boat building market nationally.
With over 30 years of experience, we offer the finest craftsmanship and boat building knowledge for any woodworking project. As a Scandinavian trained yacht builder relying on vast experience gained in the finest boat yards on the West and Gulf Coasts, we can efficiently complete all types of projects with an artisan's touch.
- Yacht Carpentry
- New Yacht Construction
- Classic Mahogany Runabout Construction,
- Museum-Quality Antique Wooden Boat Restoration
A Message
Experience , the difference, through craftsmanship, craftsmanship, through experience.
- Wooden Yachts
- Mahogany Runabouts
- Custom Boats
Craven Boatbuilding Fine Yacht Woodworking/ Carpentry
As boat builders carrying on the centuries-old craft of fine yacht joinery and yacht aesthetics — instead of house carpenters or cabinet makers who have adapted their craft to boats —clients can trust the finished product will be both beautiful and lasting, even in the most extreme sea conditions. With over 25,000 miles of blue water sailing experience, we know how to design and build for maximum functionality and quality. From minor fine cabinetry and repairs, to new custom boat construction, our skills and experience let us professionally manage and complete any project.
Please contact Craven Boatbuilding for an initial consultation or with any further questions.
Craven Boatbuilding
1001 Sue Dr, Ste. C2
Kemah, TX 77565
(713) 924-7746
Copyright 2014. Craven Boatbuilding. All rights reserved.
Most Complete List Of Suitable Wood For Boat Building

Wood is an organic material that has been used by humans since ancient times. So it is natural and It comes to us from nature. Many products have been produced using wood from the past until today, and the field of use is still expanding.
A common view is that the widespread use of synthetic materials will reduce the use of wood, but this view is not correct. If calculated based on the individual, the amount of wood consumption is increasing day by day. Of course, the most important factor here is that the wood material has very efficient and superior properties.
Today, wood is used in at least 6,000 different areas. Of course, the topic that attracts our attention here is the construction of wooden boats . Plywood is the first material used to build a wooden boat.
Boats and yachts made of the highest quality wood and precisionist attract attention and are very popular in wider circles.
read more: Thermowood Facade

One of the most important woods used throughout history to build ships and boats is oak wood. Oak wood has a very compressed and strong tissue so it is mentioned as a symbol of strength and endurance in ancient literary texts.
This wood is relatively hard and heavy, has a high resistance to erosion and moisture, and these properties have made it the most suitable wood for building the hulls of commercial ships, warships and boats.
Table of Contents
materials used in boat building
- Epoxy Resin
- Polyester Resin
- Marine Grade Plywood
- Marine Grade Paint
- Marine Grade Carpet
- Marine Grade Vinyl
- Marine Grade Fasteners
- Marine Grade Adhesives
- Marine Grade Sealants
- Marine Grade Hardware
- Marine Grade Electrical Components
- Marine Grade Lighting
- Marine Grade Fuel Tanks
read more: Mindi Wood
Special Wood Characteristics for Sailboat Construction
Wood material stability.
The wood materials used in sailboat construction should possess high stability and be protected against tree pests. The fundamental rule is that regardless of the type of wood material chosen, it should be thoroughly dried and reduced to a specified moisture level.
As evident, it is necessary for wood materials to be as stable as possible because wood exhibits expansion and contraction in specific directions during moisture exchange. Furthermore, by extracting the sap inside the wood to prevent insect attacks and moisture-induced decay, preservation can be achieved.
Suitable Wood for Shipbuilding
When selecting wood, the primary raw material in shipbuilding, the criteria mentioned above should be taken into consideration. However, with technological advancements, the use of wood materials with increased durability has led to an extended lifespan of ships and reduced maintenance costs.
Before commencing the production phase, after determining the quantity of wood materials to be used in different parts of the project, the types of wood should be specified based on their intended usage.
It is preferable that elements acting as walls, especially in the internal partitions of boats and ships , be produced from sandwich panels and similar materials, as this helps reduce the vessel’s weight. Additionally, the high modulus of elasticity of sandwich panels enhances the structural strength.
What wood is better for boat building?
There are several main factors that determine the type of wood used in boat construction . The most important criterion for choosing are the life span, strength, weight and elongation coefficient of the wood according to the humidity and temperature of the air and its tendency to twist.
The wood used in boat construction should be dried and has approximately 15% moisture.
Similarly, if the wooden boat used in the hull of the boat is thrown into the sea, if it absorbs water, it will try to create large forces. For this reason, especially in the body part, types of wood with low elongation coefficient should be used and the wood should be well protected against the effects of water.
read more: Wood Products Care & Maintenance Instructions
It has a wide dispersal in the world. Species of crowned trees that can reach 25 meters in height and 2 meters in trunk diameter. The stem of these plants is smooth, its skin is first smooth and then thick, and it is brown in color.
Its roots go far and deep. The leaves as well as their form can be different, they are clustered, jagged or direct-edged.
Its cylindrical fruits called “bonito” are placed in a glass. Some species have large oaks. Its wood is durable. This is the best wood for making backbones. It is mainly used in the construction of the backbone and also in interior decoration.

best wood for boat building
The best wood for boat building depends on the type of boat being built . Cedar wood and mahogany wood are popular choices for wooden boat building, as they are both lightweight and rot-resistant. Plywood is also a common choice, as it is relatively inexpensive and easy to work with. Other woods, such as oak and teak, may be used for specific boat-building projects.
hornbeam, as a shady tree, prefers soft, fertile and moist soils. It has a shallow root system that expanded laterally. It has the feature of re-sprouting when cut. With proper pruning, it is used as a long hedge in landscaping works. Its wood is heavy and hard, that’s why it is used in making tools and construction works. Firewood is very suitable because it works slowly and emits a lot of heat.
It can be used as a last choice instead of the trees above.
read more: Finger Joint Wood Board
Yellow Pine
It is generally used as a support part for the outer covers of yachts, deck floors and is one of our native trees.
American Mahogany: Also called Honduran Mahogany, this wood has been used in the construction of yachts for many years. Often used in wooden floors, decks, cabin linings, etc.

Another wood that has received a lot of attention in the boat building industry is mulch wood . This wood has a coarse tissue and is placed in the group of heavy and semi-heavy woods, and since it is resistant to bending, it is very suitable for use in boat building.
Boat Building Wood
Sapele, Mahogany, Oak, European Pine, and Pine – these are classic boat-building woods . Most frames are made of oak. In the past, boats were often covered with oak wood. But what wood is used for boat building now? Primarily mahogany. It has the best strength-to-weight ratio and is resistant to water for boat construction. If you’re looking for marine wood for your boat, you’re in the right place. Contact our experts.
Wood in shipbuilding:
Chestnut wood.
in terms of wood, it is very similar to oak. The outer wood is narrow, the inner wood is wide. The circle is porous. The tissue of the spring is porous, where the trunk can be seen. It is invisible with its pores in the fall tissue. The core rays are invisible, which is the most important feature that distinguishes it from oak. It’s tough, it is built hard. Flexible and easy to break. It is easy to bend because it has long threads. It is easy to handling. It is resistant to the destructive effect of air. It paints very well.
It has great strength underwater. The nails stick together well with glue. It is a tree that can be used as a substitute for oak to make the backbone.

teak wood : In-deck covers, despite the difficulty of processing, it is preferred due to its high resistance in heavy conditions and water resistance. It is imported wood so it is expensive.
wood used in ship building Te ak is the most common type of wood used in ship building . Te ak is a tropical hard wood that is known for its strength and durability . It is also resistant to rot , decay , and term ites , making it an ideal choice for ship building . Other types of wood used in ship building include oak , mah og any , and pine .
What should the structure of a recreational wooden boat be like?
The structure of a recreational and sailboat should be constructed using waterproof wood. It should be protected against various wood pests and, for complete safety during the journey, should be resistant to mechanical damage.
Since wooden boats are used at sea , they are exposed to external conditions such as sun, rain, seawater, wave force, wind, etc. They are exposed to many negative factors. Therefore, in order for them to serve for many years, they must be structurally intact and high-quality materials should be used in their production.
read more: AgarWood
If you have any experience with this type of wood, share it with us in the comment section below. We will answer your questions about wood species.
Related Posts

What is the World’s Strongest Wood?

Timber Ireland – Buy Building Supplies Online

Questions To Ask Your Wood Supplier
Leave a reply cancel reply.
Your email address will not be published.Required fields are marked *
Hit enter to search or ESC to close

Yacht Construction Expertise
Please refine your search or simply email us or call 1 954 525 5111 and we'll immediately put you in contact with one of our yacht specialists to discuss your enquiry.
ADVANCED SEARCH
- ABOVE 400'-200'
- MID RANGE 200'-150'
Luxury Yacht Construction Expertise
New yacht construction expertise requires years of working closely with the world’s largest and best shipyards. With over 60 new luxury yacht projects completed, not including those in progress, we represent the most discerning clientele in the industry, and have been thoroughly involved in some of the world’s largest yacht transactions. We are confident in our ability to help you create the ultimate luxury yacht that meets your specific needs and expectations. When you have dedicated yachting specialists working for you, and representing your best interests, the feat of building your dream becomes reality.
Related Yacht Ownership | Build Your Own Yacht

Merle Wood & Associates has over 150 years of combined experience in new yacht construction. This vast experience ensures that our clients benefit by having the most comprehensive build specifications, the most thorough design specifications, the most competitive price, and that the most appropriate shipyard is selected for their project.
Relationships
While we have established relationships with all major yacht builders around the world, we do not represent any shipyard directly which means we’re able to take an unbiased approach in assisting our clients with selecting the right shipyard based on their personal requirements, resulting in the best possible build.

Given our expertise and the sheer number of new build projects we have on record, yacht builders work harder to win the business of our clients, because they know we understand how to bid and we also have relationships with their competitors. Due to our clout and the amount of future business we will bring to bear, shipyards know it’s imperative to keep our clients happy, so that we will continue to recommend them. Thus, there is tremendous value in our representation.
Coordination
Building a new yacht can be a complex and costly event for someone unfamiliar with the process. We coordinate all aspects of the project and ensure that the right elements are in place, before, during and after construction. It is because of our luxury yacht construction expertise that luxury yacht owners turn to us time and time again.

Speak To A Yacht Construction Specialist
For more information about building a yacht or yacht construction expertise from a qualified yacht construction specialist, simply contact the luxury yacht brokerage firm of Merle Wood & Associates for assistance.
- 1-954-525-5111
- web(Contact us at)merlewood.com
- About us
I'm interested in:
Chartering a yacht Buying a yacht Selling a yacht Charter marketing Building a yacht Other
Please leave this field empty.
At Merle Wood & Associates, we focus on providing the best user experience throughout our website for our visitors. We achieve this by using cookies, which store a little information from your browser. If you would like to learn more, please see our privacy and cookies policy .
Share this page

- Yacht Search
- Charter a Yacht
- Buy A Yacht
- Build a Yacht
- Sell a Yacht

Your Name (required)
Your Message
Please call me Please email me
Your Phone (required)
CANCEL Please leave this field empty.
Post comment
or continue as guest
Explore Zheleznodorozhny
Essential zheleznodorozhny.

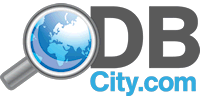
- Bahasa Indonesia
- Eastern Europe
- Moscow Oblast
Elektrostal
Elektrostal Localisation : Country Russia , Oblast Moscow Oblast . Available Information : Geographical coordinates , Population, Area, Altitude, Weather and Hotel . Nearby cities and villages : Noginsk , Pavlovsky Posad and Staraya Kupavna .
Information
Find all the information of Elektrostal or click on the section of your choice in the left menu.
- Update data
Elektrostal Demography
Information on the people and the population of Elektrostal.
Elektrostal Geography
Geographic Information regarding City of Elektrostal .
Elektrostal Distance
Distance (in kilometers) between Elektrostal and the biggest cities of Russia.
Elektrostal Map
Locate simply the city of Elektrostal through the card, map and satellite image of the city.
Elektrostal Nearby cities and villages
Elektrostal weather.
Weather forecast for the next coming days and current time of Elektrostal.
Elektrostal Sunrise and sunset
Find below the times of sunrise and sunset calculated 7 days to Elektrostal.
Elektrostal Hotel
Our team has selected for you a list of hotel in Elektrostal classified by value for money. Book your hotel room at the best price.
Elektrostal Nearby
Below is a list of activities and point of interest in Elektrostal and its surroundings.
Elektrostal Page
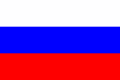
- Information /Russian-Federation--Moscow-Oblast--Elektrostal#info
- Demography /Russian-Federation--Moscow-Oblast--Elektrostal#demo
- Geography /Russian-Federation--Moscow-Oblast--Elektrostal#geo
- Distance /Russian-Federation--Moscow-Oblast--Elektrostal#dist1
- Map /Russian-Federation--Moscow-Oblast--Elektrostal#map
- Nearby cities and villages /Russian-Federation--Moscow-Oblast--Elektrostal#dist2
- Weather /Russian-Federation--Moscow-Oblast--Elektrostal#weather
- Sunrise and sunset /Russian-Federation--Moscow-Oblast--Elektrostal#sun
- Hotel /Russian-Federation--Moscow-Oblast--Elektrostal#hotel
- Nearby /Russian-Federation--Moscow-Oblast--Elektrostal#around
- Page /Russian-Federation--Moscow-Oblast--Elektrostal#page
- Terms of Use
- Copyright © 2024 DB-City - All rights reserved
- Change Ad Consent Do not sell my data

IMAGES
VIDEO
COMMENTS
Wood was the medium successful IRC raceboat designer John Corby made his name with in the 1990s and 2000s. And it was the choice of one of the UK's most successful yacht designers, Stephen Jones ...
Boat wood: a complete guide for yacht owners. Boatbuilder and finisher Lyndon March explains which types of wood work best for different repairs and modifications on board. Whether you're building a boat from scratch or making repairs, knowing which wood will work best for the job is essential. Credit: Dmitriy Shironosov/Alamy Credit: Dmitriy ...
Best Boat Wood For Boat Building. 1. Spruce. Spruce is one of the best boat woods for boat building. It is a softwood but strong and durable, making it ideal for building boats. As a softwood, working with spruce is comparably easier as the wood is bendable and easy to cut.
W ooden boat building is different from any other form of woodworking. It requires curves and angles rarely found in furniture and house construction. Boats are structures that move. Because a boat spends much of its life in water, the wood used to build it must have certain properties that give it sufficient strength, make it resistant to rot, and provide resiliency when used in conjunction ...
Many modern wood-epoxy boats are based on traditional designs but take full advantage of modern design and construction techniques to minimize weight and maximize performance. Others are full-out modern superyachts measuring over 100 feet in length and a few are flat-out race boats.
Join Bristol Shipwrights as we document and video the challenges of building a 43' Alden 270 schooner. Whether you're a professional or backyard boatbuilder, a woodworker, or a dreamer, we're confident you'll learn something new about boats and woodwork from our screw ups and successes. Help build Evelyn.
Instead, it is great for frames, handles, poles, boat hooks, and more. 3. Cypress. You can typically get your hands on cypress for the lowest cost if you live near the Gulf coast of the United States. Cypress is a phenomenal wood for planking because its natural resin is fully resistant to dry rot.
The Art of Phinisi Construction. Building a Phinisi is a meticulous process that blends centuries-old techniques with modern shipbuilding practices. Master craftsmen, often from generations of shipbuilders, guide each stage of construction. Selecting the Wood: Choosing the right type of wood is crucial. Teak, ironwood, and other hardwoods known ...
Traditional Wooden Boat Building (Plus Video) Published: April 17, 2024. Projects, Outdoor. The two craftsmen inspecting a boat under construction, showcasing the art of traditional wooden boat building. This time-honored practice merges precision woodworking skills with a deep understanding of marine architecture.
With so many composite products on the market today, the Spirit team is frequently asked about the intricacies of building modern yachts with such a traditional material. In summary, wood is the only natural boat building material offering beauty, impressive strength to weight ratio, flexibility and durability.
Sam Fortescue shines a light on boat building jargon and looks at past, present and future boat building materials ... But perhaps the best known of the wooden boatbuilders is Spirit Yachts in Ipswich, building thoroughly modern boats - in composite wood. The Spirit 44E is a 'zero carbon' cruising yacht. Credit: Richard Langdon
Teak. A native tree of the East Indies and Burma, teak is the most noble of all boatbuilding woods. Due to a natural resin within its fibers. it resists dry rot and water soakage, and even when left unfinished it appears to last indefinitely. Boats built of this wood have been known to last for centuries.
It's commonly used for planking and hull construction. Advantages of Using Wood in Boat Construction. Strength and Resilience: Wood's natural strength and ability to flex with waves make it an ideal choice for boat construction. Classic Aesthetics: Wooden boats are renowned for their classic, timeless beauty, attracting enthusiasts and ...
Cedar. Cedarwood is a great choice for boat building and has a few unique features. It contains natural chemicals that prevent rot, repel insects, and contain anti-weed properties. Cedar typically has a tight grain, making it easier to work with than other woods. There are different types of cedar as well, Red, Yellow, and Lebanon.
Learn More - Buy Plans / Jig. The C-25 is a North Carolina sport fishing boat in a trailerable center console layout. With Carolina flared bow, broken shear and tumblehome she is an iconic design. 28′ LOA (25'2″ hull) 8′6″ beam. 16″ - 18″ draft. 350hp single or twin 200hp max. Cruise 30-35mph.
Pros and Cons of Wood in Boat Construction. Aug 21, 2023. Twitter Share on facebook Email. These days "wood-free" construction is a buzzword among many boat builders, but Sean at Len's Cove Marina reminds us that the right kind of wood in the right places is still a good choice for many boating applications — though not in others. These ...
From minor fine cabinetry and repairs, to new custom boat construction, our skills and experience let us professionally manage and complete any project. Craven Boatbuilding. 1001 Sue Dr, Ste. C2. Kemah, TX 77565. (713) 924-7746. Located on Galveston Bay, Craven Boatbuilding is a full-service marine woodworking facility serving the Houston and ...
The wood used in boat construction should be dried and has approximately 15% moisture. Similarly, if the wooden boat used in the hull of the boat is thrown into the sea, if it absorbs water, it will try to create large forces. For this reason, especially in the body part, types of wood with low elongation coefficient should be used and the wood ...
For more information about building a yacht or yacht construction expertise from a qualified yacht construction specialist, simply contact the luxury yacht brokerage firm of Merle Wood & Associates for assistance. 1-954-525-5111. [email protected]. About us.
The Crossword Solver found 30 answers to "Yacht building wood", 4 letters crossword clue. The Crossword Solver finds answers to classic crosswords and cryptic crossword puzzles. Enter the length or pattern for better results. Click the answer to find similar crossword clues . Enter a Crossword Clue. A clue is required.
A residential and industrial region in the south-east of Mocsow. It was founded on the spot of two villages: Chagino (what is now the Moscow Oil Refinery) and Ryazantsevo (demolished in 1979). in 1960 the town was incorporated into the City of Moscow as a district. Population - 45,000 people (2002). The district is one of the most polluted residential areas in Moscow, due to the Moscow Oil ...
Can't-miss spots to dine, drink, and feast. Zheleznodorozhny Tourism: Tripadvisor has 1,133 reviews of Zheleznodorozhny Hotels, Attractions, and Restaurants making it your best Zheleznodorozhny resource.
Elektrostal Geography. Geographic Information regarding City of Elektrostal. Elektrostal Geographical coordinates. Latitude: 55.8, Longitude: 38.45. 55° 48′ 0″ North, 38° 27′ 0″ East. Elektrostal Area. 4,951 hectares. 49.51 km² (19.12 sq mi) Elektrostal Altitude.
In 1938, it was granted town status. [citation needed]Administrative and municipal status. Within the framework of administrative divisions, it is incorporated as Elektrostal City Under Oblast Jurisdiction—an administrative unit with the status equal to that of the districts. As a municipal division, Elektrostal City Under Oblast Jurisdiction is incorporated as Elektrostal Urban Okrug.